.jpg?width=1840&name=blog%20feature%20image%20(3).jpg)
Learn how circularity and innovation are key drivers to increasing sustainability in manufacturing from Canam CEO, Marc Dutil, and One Click LCA Carbon Expert, Travis Dahl.
Improving sustainable practices in manufacturing is becoming a key market differentiator for construction materials manufacturers. In this article, learn from industry leaders Marc Dutil of Canam and Travis Dahl of One Click LCA sharing insights on why manufacturers are thinking about sustainability, why circularity will be a key method going forward, and why forward thinking companies want to exceed, not meet, standards and regulations.
How are sustainability goals related to health and safety initiatives?
Marc shared a compelling analogy between the evolution of health and safety practices and sustainability efforts. He reflected on the shift in construction industry practices over the past two decades, highlighting that merely complying with legal requirements does not ensure safety. Instead, a proactive approach that prioritizes worker safety is essential. This same rigorous approach is now being applied to sustainability at Canam. Marc emphasized that transitioning from compliance to a genuine commitment to sustainability is crucial for meaningful change.
Travis added that both health and safety and sustainability aim to prevent future harm — whether it's physical injuries on a job site or environmental damage due to climate change. He stressed the importance of adopting a mindset that goes beyond compliance to create a positive impact.
What is the myth of recycling and how does it relate to the sustainability of construction materials?
Marc discussed the limitations of traditional recycling in the context of steel manufacturing. He shared an anecdote from his childhood about collecting bottles for recycling, drawing a parallel to the misconception that recycling scrap metal is sufficient. Marc pointed out that while recycling can prevent the exploitation of new resources, it often results in higher CO2 emissions due to the energy-intensive process of converting scrap into new steel. He argued that this process, though better than discarding materials, is still wasteful and emphasized the need to rethink our approach to recycling in favor of circularity.
Travis expanded on this idea by discussing how products can be designed for disassembly and reuse. He mentioned examples from other industries, such as reusable Coke bottles in Latin America, and proposed that the construction industry could adopt similar practices. Designing buildings for easy disassembly and reuse of components, rather than relying on recycling alone, could significantly reduce waste and emissions.
How can we design better for disassembly and circularity?
Marc highlighted the complexity of construction projects, which involve multiple layers of materials and components. He shared his experience of consulting a large recycler about deconstructing metal structures for component reuse. The recycler’s feedback underscored the challenges of reusing components due to certification and design limitations. Marc stressed the importance of designing buildings with traceability and documentation that extend beyond current legal requirements. He suggested using bolts instead of welding to facilitate easier disassembly and reconfiguration of components.
Travis echoed the importance of tracking and monitoring the performance of structural components throughout their life-cycle. He mentioned the potential use of sensors in materials like concrete to gather data on their condition, which could inform future reuse. Both experts agreed that public policy and market incentives would play crucial roles in encouraging the adoption of circular design practices.
What are environmental product declarations (EPDs) and how do they provide value to manufacturers?
Travis explained that EPDs are standardized documents that detail the environmental impact of a product over its life-cycle, including its production, use, and disposal phases. EPDs follow ISO-defined processes and are considered the gold standard for product verification. Scope 1 and 2 emissions refer to direct and indirect emissions from a company’s operations, respectively, while Scope 3 emissions encompass all other indirect emissions in the value chain, such as those from purchased goods and services.
Marc shared that Canam's first EPD provided a comprehensive baseline for understanding the environmental impacts of their products. The process of creating an EPD highlighted areas previously overlooked, such as the impact of insulation materials and coatings. He emphasized that EPDs enhance education, certification, and trustworthiness for specifiers, serving as a valuable benchmark for sustainability efforts. Marc also noted the significant proportion of Scope 3 emissions in their overall footprint, underscoring the importance of focusing on materials and their reusability.
How can organizations that grow through acquisition maintain sustainability policies if the acquired companies have no sustainability plans in place?
Marc advocated for acquiring companies with high emissions to improve their sustainability practices rather than avoiding them. He argued that providing leadership in sustainability to these companies benefits the planet and enhances the value of the acquired business. Marc emphasized that companies slow in their sustainability journey would face decreasing value and less operational freedom, making them prime candidates for transformation by committed organizations like Canam.
How do European standards impact operations in North America?
Marc and Travis discussed the influence of European standards on North American operations. Marc pointed out that Europe’s higher energy costs have driven more efficient and sustainable practices, leading to better system choices. He suggested that North America could learn from Europe’s approach to sustainability, which is often driven by economic necessity. Travis added that while European standards are more stringent, they provide a solid foundation for North American companies to build upon. He emphasized that the road to sustainability has already been paved, and North American companies could adopt these standards more easily than starting from scratch.
In conclusion, the session underscored the need for proactive and integrated approaches to sustainability, drawing parallels with health and safety practices, debunking myths around recycling, advocating for circular design, and emphasizing the importance of EPDs and global standards. The insights shared by Marc and Travis provide valuable guidance for industry professionals aiming to drive sustainable manufacturing practices forward.
How can One Click LCA help manufacturers in their sustainability goals?
One Click LCA's EPD generator is the quick and easy solution for manufacturers looking to drive their own sustainability goals. Create reliable and accurate environmental product declarations (EPDs) at scale, providing comprehensive insights into the environmental impact of products. With One Click LCA's EPD generator, manufacturers can streamline the EPD creation process, ensuring compliance with industry standards while identifying opportunities for improvement. By adopting this tool, companies can not only meet regulatory requirements but also build greater transparency and trust with customers, driving their sustainability efforts forward, and setting a benchmark for industry excellence. Embrace the future of sustainable manufacturing with One Click LCA’s EPD generator and lead the way in environmental responsibility.
Carbon Experts Newsletter
Industry news & insights — straight to your inbox
Want to learn more?
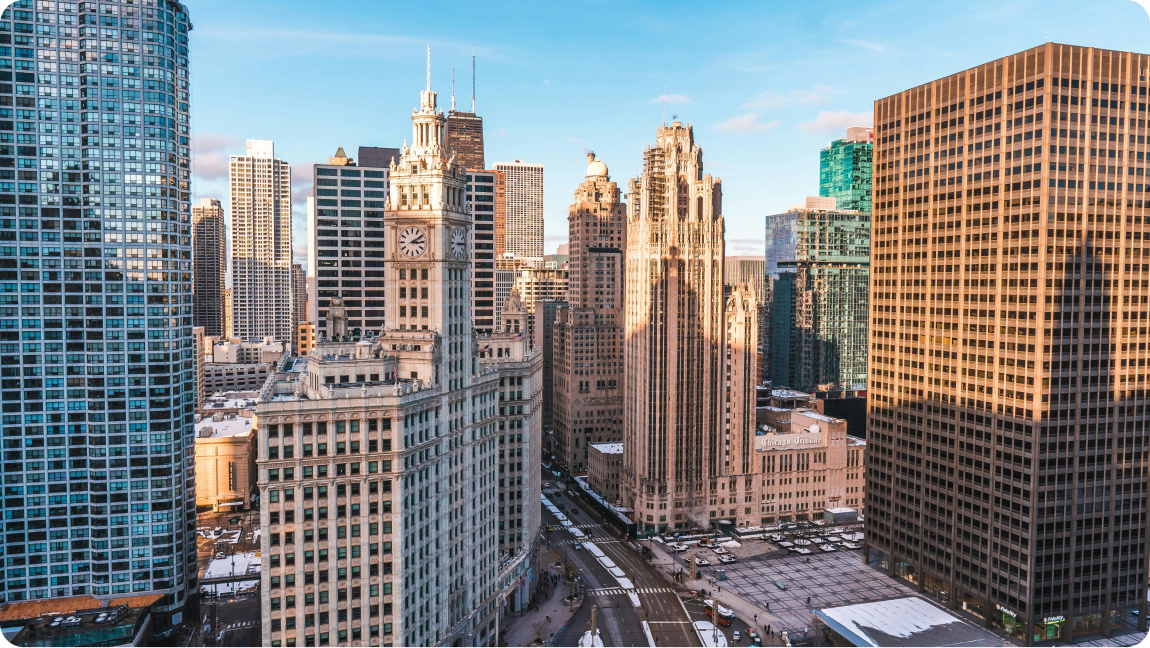
Melina Zacharia • May 22 2024
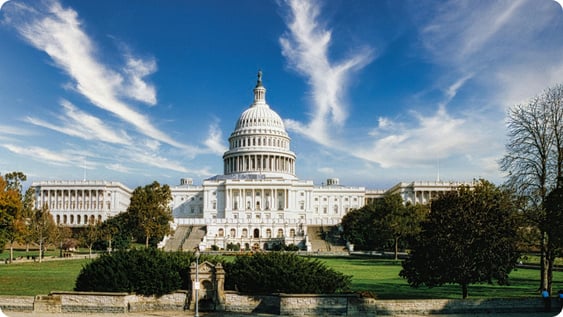
Aileen Carroll • Oct 18 2024
.jpg)
Aileen Carroll • Mar 28 2024
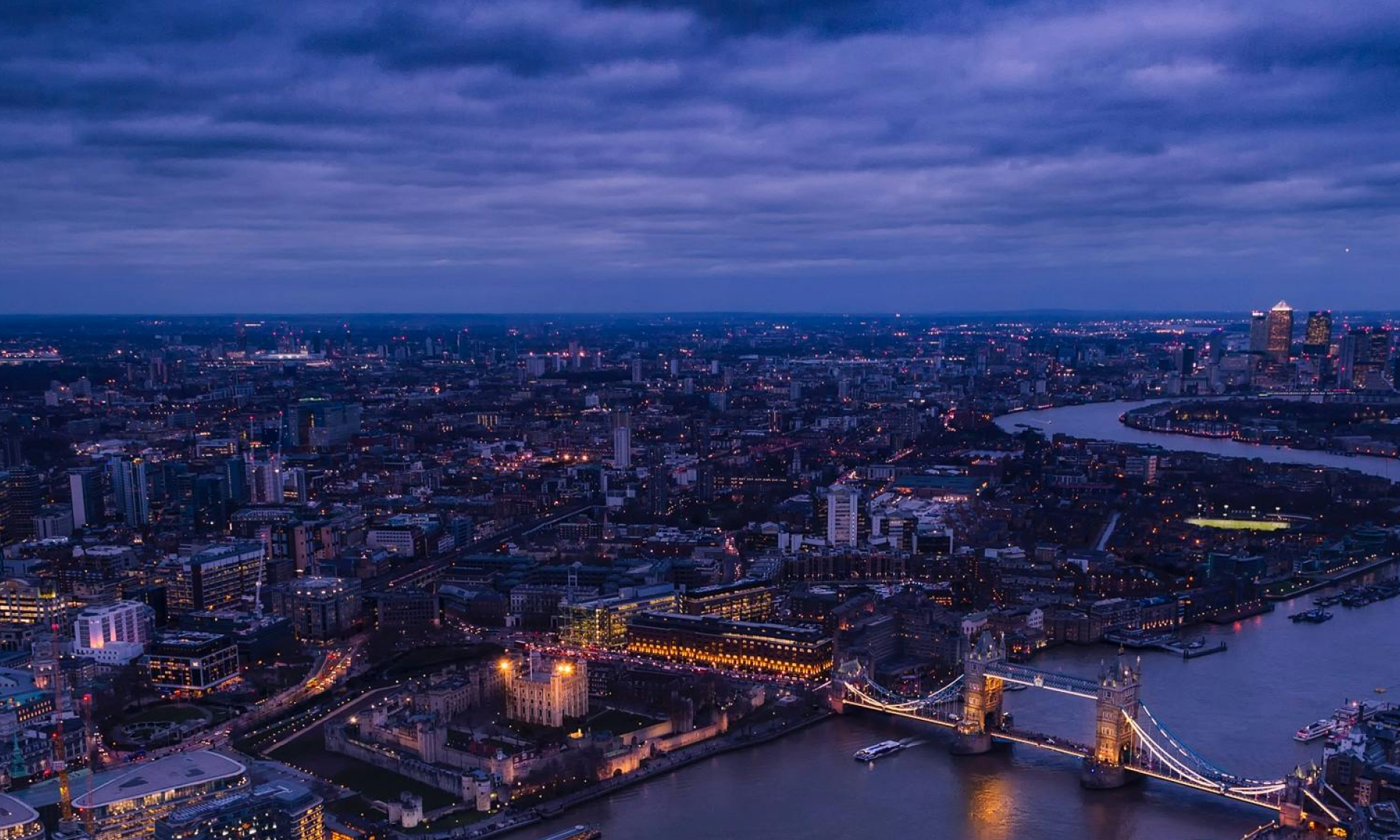
Laura Drury • Nov 14 2024