.jpg?width=1840&name=blog%20feature%20image%20(50).jpg)
ArcelorMittal applies innovative carbon-neutral steel solutions to reduce embodied carbon in construction projects.
"Enable high-performance design by using less but stronger steels for resistance-driven elements. Engage with manufacturers to understand the industry's realities and where embodied carbon lies in your project.
And most importantly: act early, collaborate, and be willing to think outside the box, as time can be the enemy of sustainability."— Marion Charlier, PhD, Advanced Building Solutions and Sustainability Lead at ArcelorMittal
Understanding the carbon emissions related to steelmaking
There are different ways of manufacturing steel, and each steelmaking route has its own carbon footprint. Here are some examples for sections:
- Blast furnace-basic oxygen furnace (BF-BOF): The main inputs are iron ore and coal. The iron ore is present as an iron oxide, and the oxygen needs to be removed. To do so, coal is used as a reductant. This is why this production route is quite intensive in terms of carbon emissions, with the worldwide average roughly between 2.25 / 2.8 t. CO2/t.
- Direct reduction iron (DRI) followed by an Electric Arc Furnace: The main inputs are direct reduced iron (sponge iron) and natural gas. The main carbon emissions of this production route come from the use of natural gas as a reductant to remove the oxygen as well as from purchased electricity. The worldwide average of emissions is roughly between 1.12 / 1.35 t. CO2/t.
- Electric Arc Furnace (EAF): The main input is steel waste, also called scrap. This waste can come from the construction industry or any other type of industry. Steel is easy to separate from other waste because of its magnetic properties. An electric arc melts the scrap and manufactures it into steel again because steel can be recycled over and over without losing mechanical properties. The main carbon emissions here are from purchased electricity. The worldwide average of emissions is roughly between 0.62 / 0.85 t. CO2/t.
Depending on how your steel products are made, there are different ways of approaching the decarbonization of your projects.
XCarb®: Towards carbon-neutral steel
XCarb® brings together all of ArcelorMittal’s initiatives aiming to decarbonize our steel production. It is in alignment with the goals of the Paris Agreement and the EU Green Deal by committing to reduce CO2 emissions by 35% by 2030 in Europe and be net-zero by 2050.
ArcelorMittal’s XCarb® innovation fund, which invests in companies developing breakthrough technologies that accelerate the steel industry’s transition to carbon-neutral steelmaking, is part of this.
XCarb® recycled and renewably produced — available EPDs
Additionally, XCarb® recycled and renewably produced steel is manufactured using the electric arc furnace process, powered by electricity from renewable sources, with up to 100% scrap. For example, the sections that are manufactured in Luxembourg use 100% scrap and 100% green electricity.
In doing so, the CO2 per tonne of finished steel is brought down to 333 kg, which is significantly lower than the average for the global steel industry today. In addition, other products are available in XCarb® recycled and renewably produced with specific environmental product declarations (EPDs): sheet piles, rebars, hot rolled coils, Magnelis ®, heavy plates, and structural hollow sections providing a complete range of carbon-neutral steel construction products.
ArcelorMittal's path towards carbon-neutral steel production
Learn more about how innovative carbon-neutral steel solutions can decrease embodied carbon on projects.
The importance of design for the project building LCA
A couple of years ago, questions related to sustainability and how steel materials are manufactured were very rare, but now, these kinds of questions are the most common. What’s driving the shift is that more regulations are being implemented. In countries with regulations that specify embodied carbon thresholds per square meter, customers, engineers, architects, and designers all need to consider those constraints at an early stage.
Choosing low-carbon-emissions materials is important, but it is not sufficient. As architects and structural engineers, this needs to be coupled with clever design to reduce the carbon footprint of the project further. For example, when it comes to making the superstructure lighter, a simple yet effective measure is to use higher steel grades where relevant. Another example is using cellular beams, which have holes in their web and can help reduce the total height of the building and its weight and carbon footprint. Intelligent material selection, including carbon-neutral steel, makes all the difference.
Example of intelligent material selection and its impact
Tapping into Steligence® engineering
The Steligence® engineering department at ArcelorMittal works closely with all stakeholders of the construction chain, from investors to steel fabricators, to advise and deliver cost-effective, innovative, and sustainable solutions via our Steligence® Network. Free technical assistance is also offered worldwide from structural concept design and value engineering to delivery to the site. This includes support with composite systems, structural fire engineering, LCA, FEM modeling, technical committees, etc.
Reducing embodied carbon of a project using carbon-neutral steel
To reduce the carbon footprint of a project with steel, we recommend enabling high-performance design. Do not overdesign. Use less but stronger steels. Understand where the embodied carbon is in your project by using a hotspot analysis because some elements will be an “easier win” than others. Since embodied carbon in steel production varies depending on how it is made, talk to suppliers about the supply chain and request EPDs. Remember that not all EPDs are equally transparent or comparable, so take time to understand them and look for reliable low CO2 EPDs. Finally, support entities with a robust industrial roadmap, showcasing a real (short-term & long-term) climate commitment.
How to reduce the footprint of a project with steel
One Click LCA on the path to sustainable industry
ArcelorMittal uses One Click LCA regularly in-house within our R&D team and Steligence® Engineering department. We use the software to create LCAs quickly and easily for the projects we work on, as well as to run sensitivity analyses within the research framework to become more aware of certain areas where structural systems can be deployed.
One Click LCA is the world-leading end-to-end sustainability platform for construction and manufacturing. The software platform decarbonizes and drives sustainability across the construction value chain with scientific, easy-to-use, automated life-cycle assessment (LCA) and environmental product declarations (EPDs) to calculate and reduce the environmental impacts of building, infrastructure, and renovation projects and products. The platform also allows assessment of circularity, life-cycle cost, and biodiversity.
Carbon Experts Newsletter
Industry news & insights — straight to your inbox
Want to learn more?
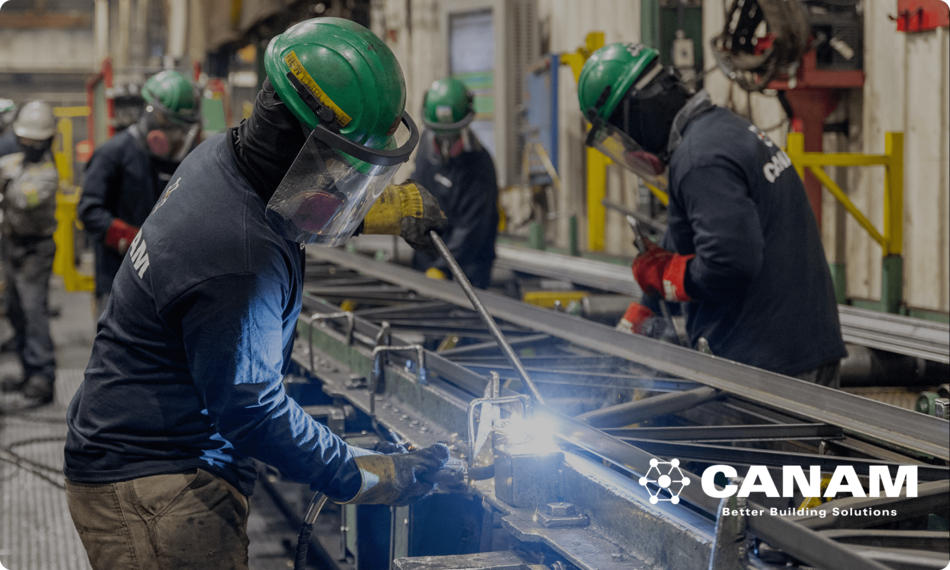
Aileen Carroll • Oct 31 2024
Asha Ramachandran • Feb 08 2024
Laura Drury • Mar 12 2024
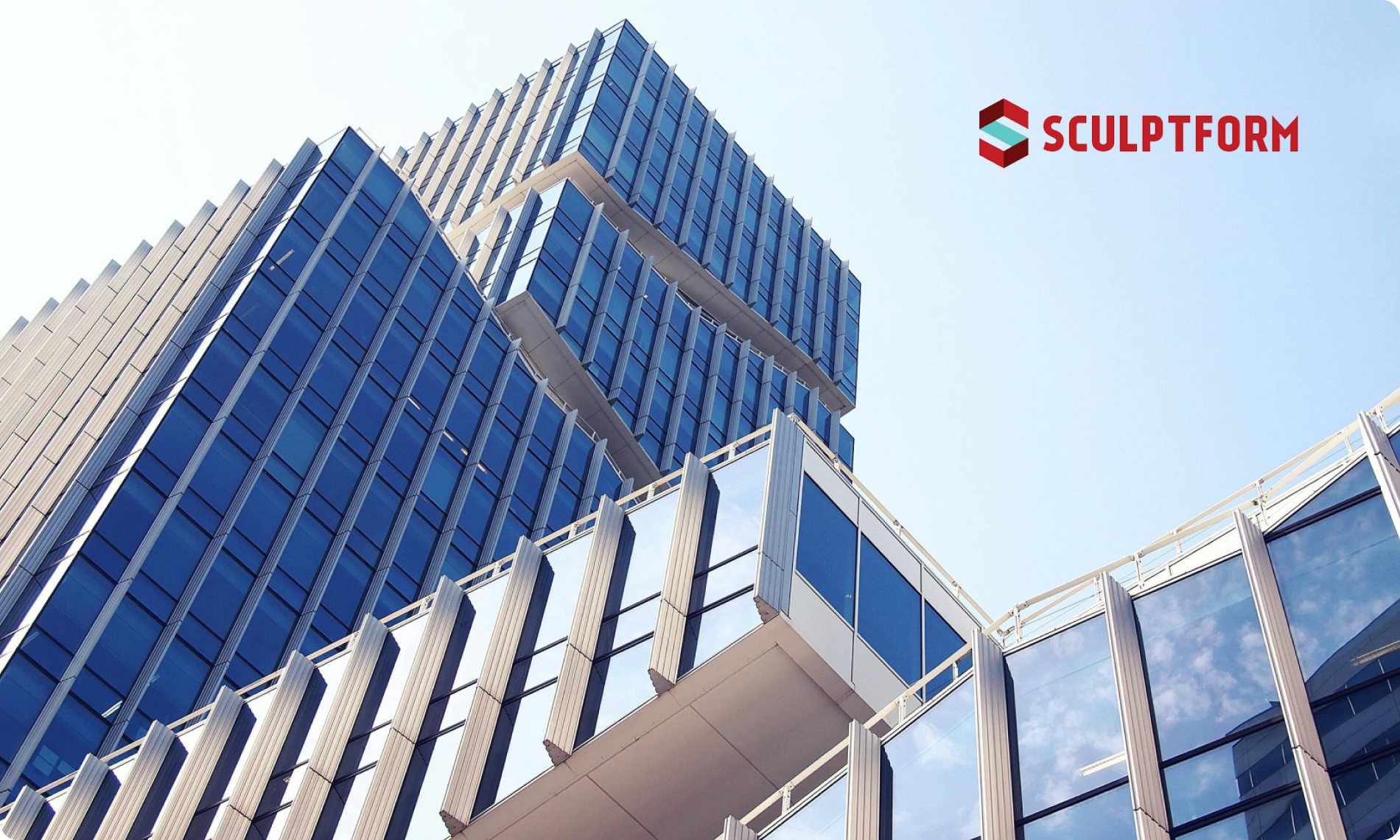
Laura Drury • Nov 26 2024