.png?width=1840&name=Buro%20Happold%20(2).png)
Sustainability expert Buro Happold shares insights on their LCA best practices and implementation strategies.
Section 1: Background to your LCA practices
What is the primary driver for performing an LCA in your projects?
Sustainability and net zero reporting are the primary drivers for performing ‘full LCAs.’ LCAs tend to be carried out for BREEAM 2018 compliance, UKGBC Advancing Net Zero (ANZ) reporting, GLA Whole Life Carbon (WLC) assessments, and supporting clients in setting embodied carbon baselines/targets. We also carry out high-level calculations of embodied carbon at the earliest stages of a project – the drivers include highlighting embodied carbon-saving opportunities early and raising awareness of the subject with the design team and client.
At what stage of your project do you typically perform an LCA?
Typically on a design project, we begin One Click LCA calculations from RIBA Stage 2. This is generally required for BREEAM and GLA WLC reporting. We generally present our capabilities on embodied carbon modelling at the bid stage and identify key material efficiency principles at RIBA Stage 1. Several of our teams (e.g., structures, facades, infrastructure) have in-house toolkits for estimating embodied carbon at Stages 1-2 for comparing different strategies.
How often do you perform LCA iterations throughout a project?
LCAs are often performed at RIBA Stages 2, 3, and 4. However, we have projects where we have done as-built LCAs at RIBA Stage 6 and provided quantitative advice to clients during RIBA Stage 5 construction. The LCA calculations continually evolve as a more detailed system and supply chain information become available.
Which point during the design process is the best time to explore low-carbon design strategies? And which point is the best time to implement them?
Section 2: Technical details of your LCA practices
What common strategies do you use to reduce embodied carbon in your project (viewing from your discipline’s perspective)?
Example Buro Happold strategies:
General
- Refurbishment rather than new-build!
- Material efficiency discussions at every stage of the project
- Minimising finishes / exposed materials and service
- Design for durability (less need to replace)
- Local material sourcing
- Use of reclaimed materials and components
- Demolition waste utilised on adjacent plots providing it with a second life
- Open cuts for basements reduced temporary work
Structures
- Utilising an efficient structural grid to reduce demand on the structure (e.g. allowing slab thicknesses to be reduced)
- Reduce design loadings, reduce finishes weight (and extent of finishes), reduce basements, remove transfers, design for material efficiency (high utilisations)
- Low carbon cement replacement in substructure / superstructure in cement mix and recycled binders
- Use of recycled materials (e.g. recycled reinforcement steel)
- Use of Cross Laminated Timber
Facades
- Try to reduce the number of facade types, panelisation, and complexities which would increase embodied carbon
- Incorporate design for disassembly strategies so materials can be more easily reused, repurposed, or recycled
- Coordinate with the structure to optimise the setting out, movements, and facade weight to optimise carbon reductions
- Increasing recycled content of metal components
- Specifying glass that can incorporate more cullet as well as be more easily recycled at the end of life
- Coordinate with the architect to try and specify higher limits for visual tolerances and defects and to consolidate facade mock-ups
- Specify off-site assembly processes where feasible to allow for better quality control and less waste
- Coordinate interfaces during design to reduce waste and errors requiring to dismantle and repairs
MEP
- Good practice ventilation strategies such as decentralised, local systems help reduce the amount of centralised plant required
- Centralised systems for heating and cooling, when they contain refrigerant, as opposed to local refrigerant based systems
- Specifying hydronic systems (i.e. ASHP) instead of refrigerant based systems (i.e. VRF)
- Specifying low and ultra-low GWP refrigerants
- Specifying PV with lower embodied carbon
- Prolonged MEP lifespans
- Limited use of suspended ceilings
- Minimal use of raised access flooring
Are there any typical materials/products/systems specific to your discipline that, if installed, will always result in embodied carbon reduction compared to a baseline building?
I would be cautious to point to anything that “always” provides a saving! Embodied carbon is an ever-evolving field, and there is a high level of variability depending on the inputs/assumptions made. More generally, our work with C40 Cities on the clean construction hierarchy (below) sets a useful framework for high-level principles around embodied carbon. For example, using repurposed materials or less can help achieve large savings.
How do you communicate any potential design changes to the client that will reduce the project’s embodied carbon?
Diagrams illustrating the embodied carbon saving of design changes – e.g., graphs & supporting 3D images. Also, graphs illustrating embodied carbon breakdown in different options and potential savings and comparisons targets in the industry.
What are the common ways of convincing your client to adopt low-carbon design strategies?
Following the above, showing this information together with cost and programme savings is typically most impactful for incentivising real change. Reporting on the position against industry targets (e.g. UKGBC/LETI) is also helpful.
How do you ensure that any identified carbon reduction strategies are being implemented during construction?
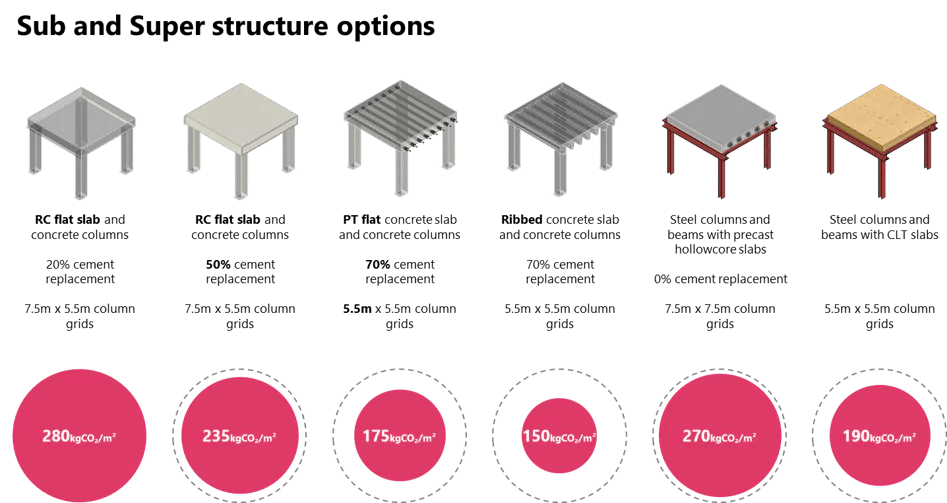
Section 4: Case studies
Are there any case studies in which you achieved an embodied carbon reduction with any of the above-mentioned strategies that you would like to share?
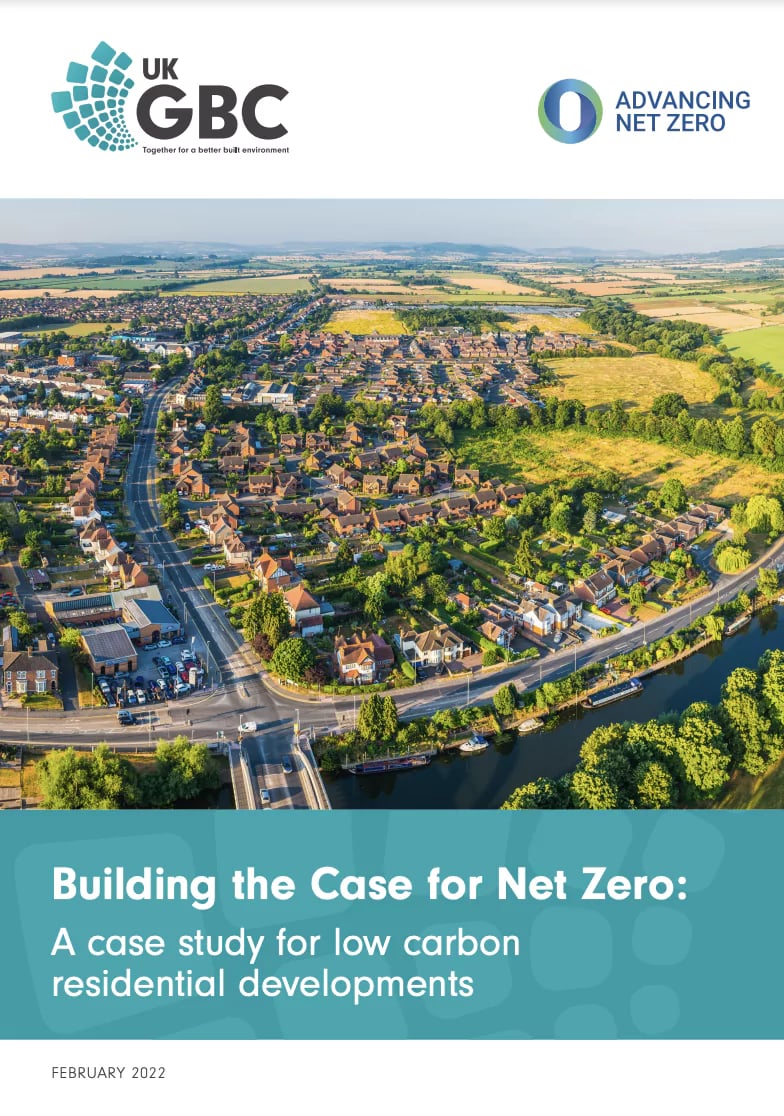
Carbon Experts Newsletter
Industry news & insights — straight to your inbox
Want to learn more?
Aileen Carroll • Mar 20 2025
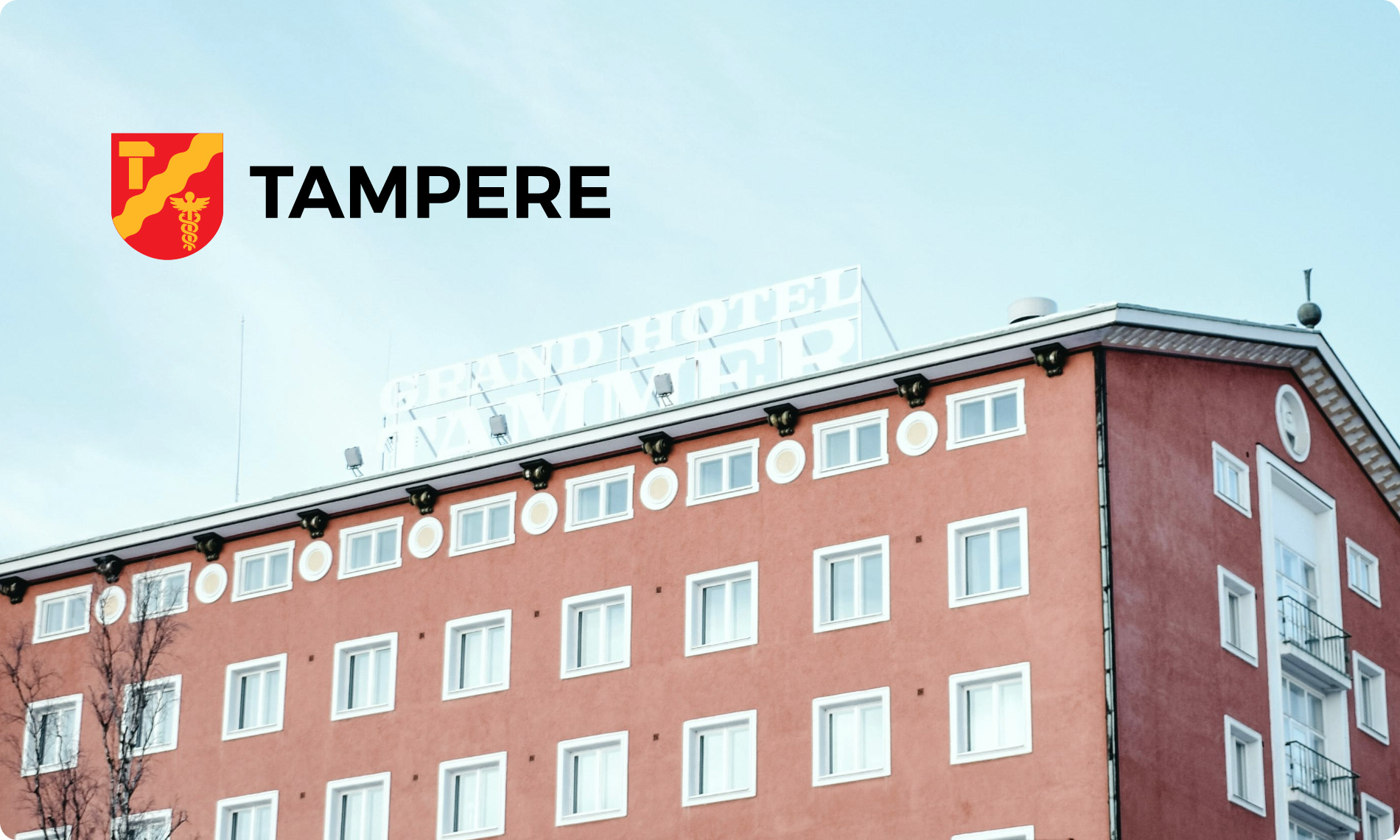
Kim Koivula • Mar 24 2025
Anna Zahrmann • Jul 04 2024
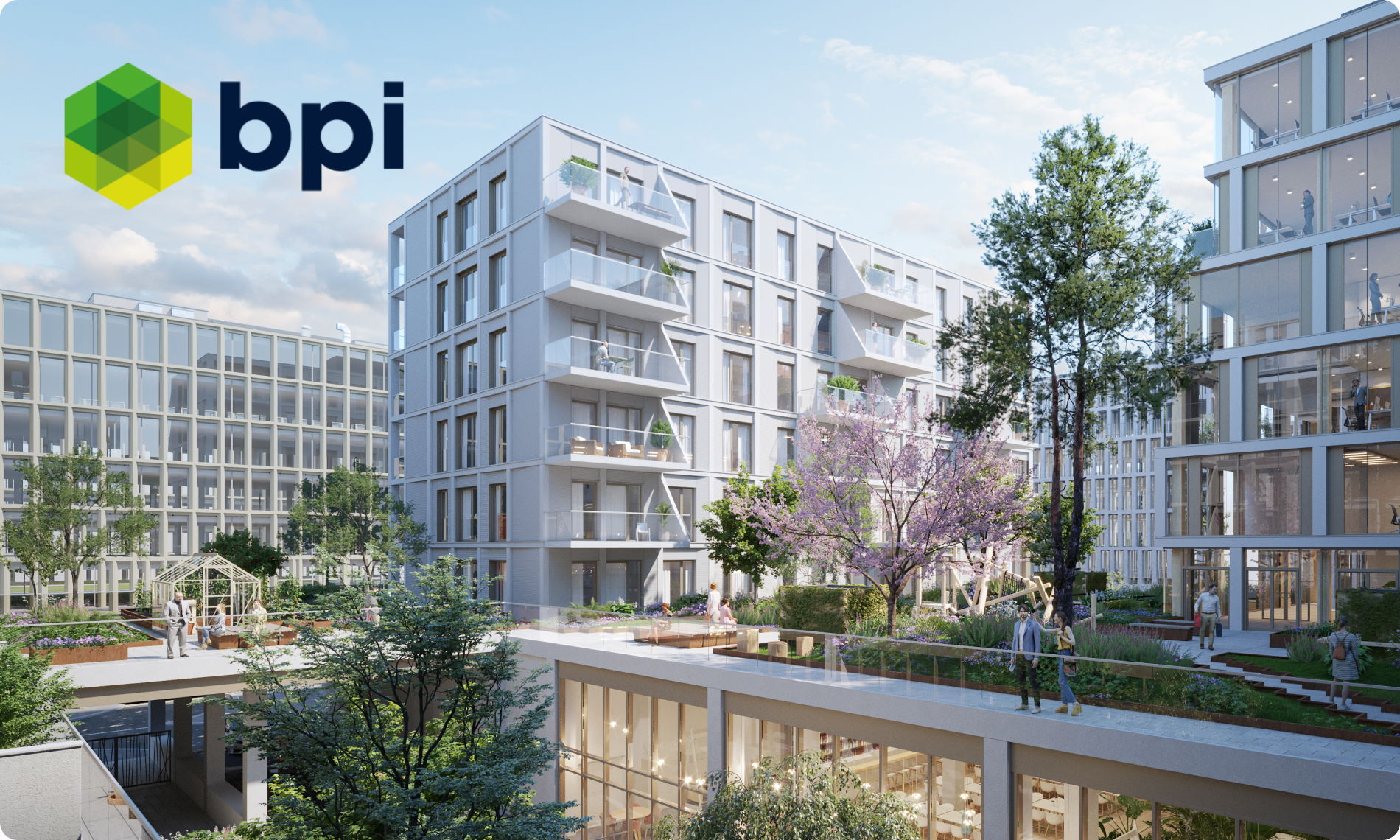
Anna Zahrmann • May 13 2025