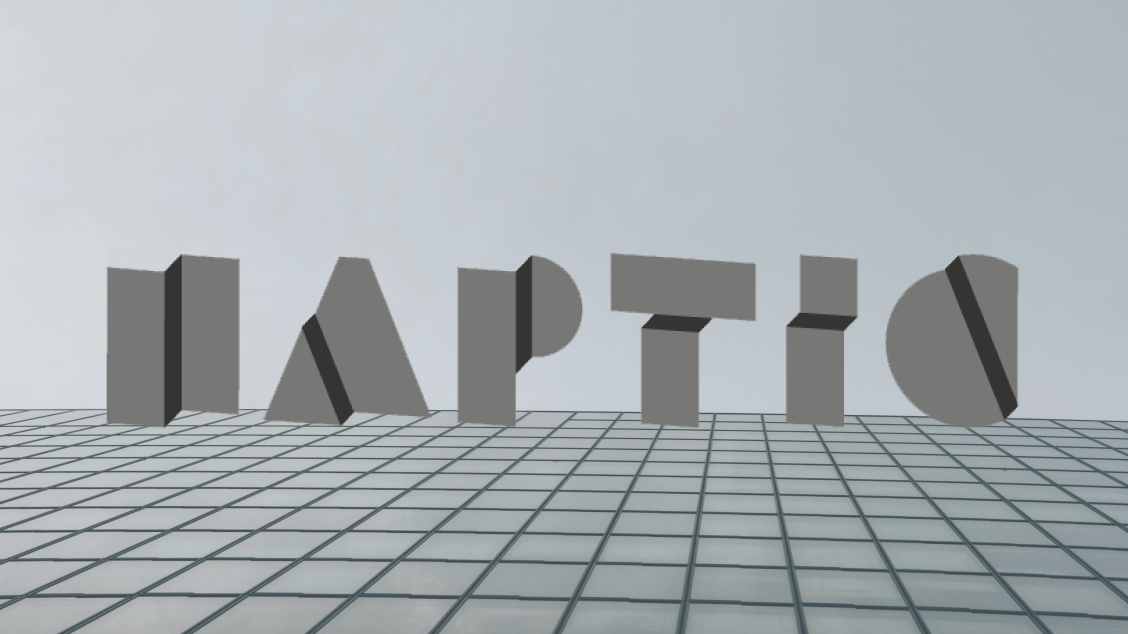
”One Click LCA is a trusted, industry-standard tool for assessing and analysing the embodied carbon within every type of material that we consider within our designs. It has been a significant enabler for us to embed sustainable architecture into our projects from the critical early stages. Something which is imperative to us, and our clients.”
– Jack Penford Baker, Associate
Driving forward modern sustainable architecture
Haptic is a London, Oslo, and Bilbao based architectural studio, established in 2009. They work across a wide range of building typologies, including workplace, urban design, residential, mixed use, hotels, and private dwellings. Conceptually driven, inspired by nature and sustainable architecture, their approach blends aesthetics and human interaction for ultimate design acclaim.
Haptic chose One Click LCA as the industry-standard tool for embodied carbon assessments, to leverage its material database for the project analysis environmental performance data, allowing for carbon analysis to inform early decision making.
Haptic Green – an integral initiative for sustainable architecture
Sustainable design is a fundamental part of Haptic’s ethos, and something that is embedded into their process from start to finish through their Haptic Green initiative.
Haptic Green leads Research and Development in the practice and is focused on environmental and social sustainability. Haptic Green directly supports the Haptic ethos of creating places that make people happy. As a think-tank, Haptic Green crosses disciplines: architects, engineers, academics, and consultants, collaborating with a wider industry network. Its purpose is to ensure that Haptic projects always consider their relationships to people and planet. Haptic Green has 5 overarching focuses:
- Design
- Internal Knowledge Sharing
- Practice Operation
- Research & Development
- Academia
A Sustainability Consultant is included in the core project team from an early phase, and plays a key role in ensuring their goal of creating an ‘Exemplar Sustainability Building’ is met through their key sustainability principles:
- Minimise demolition, maximise retention, and reuse of the existing building — reducing embodied carbon.
- A ‘low carbon first’ approach to new material choices, everything from the new structure down to wall finishes.
- Adopt passive measures to cooling, heating and ventilation, and create a high performance façade — reducing operational carbon emissions.
- Increase biodiversity and ecology on the project site.
- Design for circularity. Maximise reuse of any waste material, and consider future disassembly.
- Create high-quality internal spaces that consider the health and well-being of its occupants
300 Gray’s Inn Road: Giving a new lease of life to a tired, unsustainable, London office building
The Project:
300 Gray’s Inn Road is a 1970’s office building 500m south of Kings Cross Station. The existing building is an 8-storey block with a lower 3-storey block to the east, and is tired, deteriorating, and out of date. Additionally, with an EPC rating of ‘D’, it will become unlettable due to the EPC/MEES legislation coming into effect in 2027. The appearance is not in line with the surrounding developments, and the internal office space is far from the quality expected in the surrounding area. However, the building sits within a rich, vibrant location, and provides an opportunity to be transformed into an aesthetically pleasing, sustainable, and commercial landmark for the wider Knowledge Quarter.
The goal for 300 Gray’s Inn Road is to create an exemplar in low-carbon retrofit for London, with a target completion date of 2026.
The challenge: designing for sustainability beyond statutory requirements
The key challenge for the team working on 300 Gray’s Inn Road was to create a design that transformed the existing building, but also aligned with their retention-first strategy and commitment to targeting beyond the statutory requirements for sustainability and carbon impact. The solution was to focus on developing an entirely new façade for the building, while maintaining 88% of the internal structure. The design, manufacturing, and installation of the façade was therefore the focus for the team when identifying and implementing opportunities to reduce embodied carbon impact.
One Click LCA enables delivery of ambitious embodied carbon targets
Haptic chose One Click LCA as the tool to enable and support their initiative for design projects that had embodied carbon considerations from the early stages. In the London Plan Guidance, the GLA suggests that 17% of all A1-A5 emissions for commercial offices will come from the façade, one of the highest contributing elements after the superstructure. With the structure retained, the façade becomes the key target. As a result, the initial Stage 2 focused in detail on typical bays for the commercial and residential façades, with targets outlined based on the A1-A5 target.
This is where One Click LCA was brought in as an enabler, helping the team break down the elements of the facade bay into specific typologies during Stage 2, and to make detailed assessments about potential embodied-carbon hotspots and opportunities for incorporating different materials.
To ensure clear, transparent and robust outcomes to guide further design, the Stage 2 Report uses detailed embodied carbon analysis through One Click LCA at component level, focusing on the most critical elements in order to evaluate the relevant opportunities for improvement during Stage 3. A full WLC Assessment will be undertaken at Stage 4 when there is sufficient resolution to provide robust global results for the development.
The new façade will combine glass-fibre reinforced concrete (GRC), masonry, and some elements of precast concrete. Part of the vision outlined for the project is to ensure the new façade is holistically high performing, which means low embodied carbon but good thermal performance, passive solar gain, and natural ventilation capabilities. This is important to justify the removal of the existing façade which has poor environmental performance.
For the commercial element, the typical bays (1A + 1B) account for approximately 40% of the total development, and their build-up is representative of the majority of the commercial development. The build-up currently assumes a rainscreen façade system with steel SFS and GRC cladding. Focusing on Bay 1A, the A1 – A5 Upfront Embodied Carbon is estimated at 82.3 kgCO2/m2 which is 20% below the element level target identified.
The highest contributing elements are known as hotspots. In the typical commercial bay build-up, the top 3 contributors account for 79% of total A1-A5 façade emissions. The top 5 most carbon intensive elements are:
- GRC façade cladding
- Aluminium frame window
- Rock wool insulation panel
- Light gauge steel for façade infill
- Aluminium perforated sheet
For each of the highest contributing elements a series of alternative build-ups were explored, utilising One Click LCA to review sustainable alternatives at a quantifiable level enabled the team to see where improvements could be made in the later stages.
Conclusion
Using One Click LCA for the 300 Grays Inn Road project, the team at Haptic was able to embed sustainability principles from the early design phase, and achieve the outcome of better embodied carbon visibility and material comparability. This approach to design, in line with the Haptic Green initiative, is helping them set a new standard for sustainable design.
Carbon Experts Newsletter
Industry news & insights — straight to your inbox
Want to learn more?
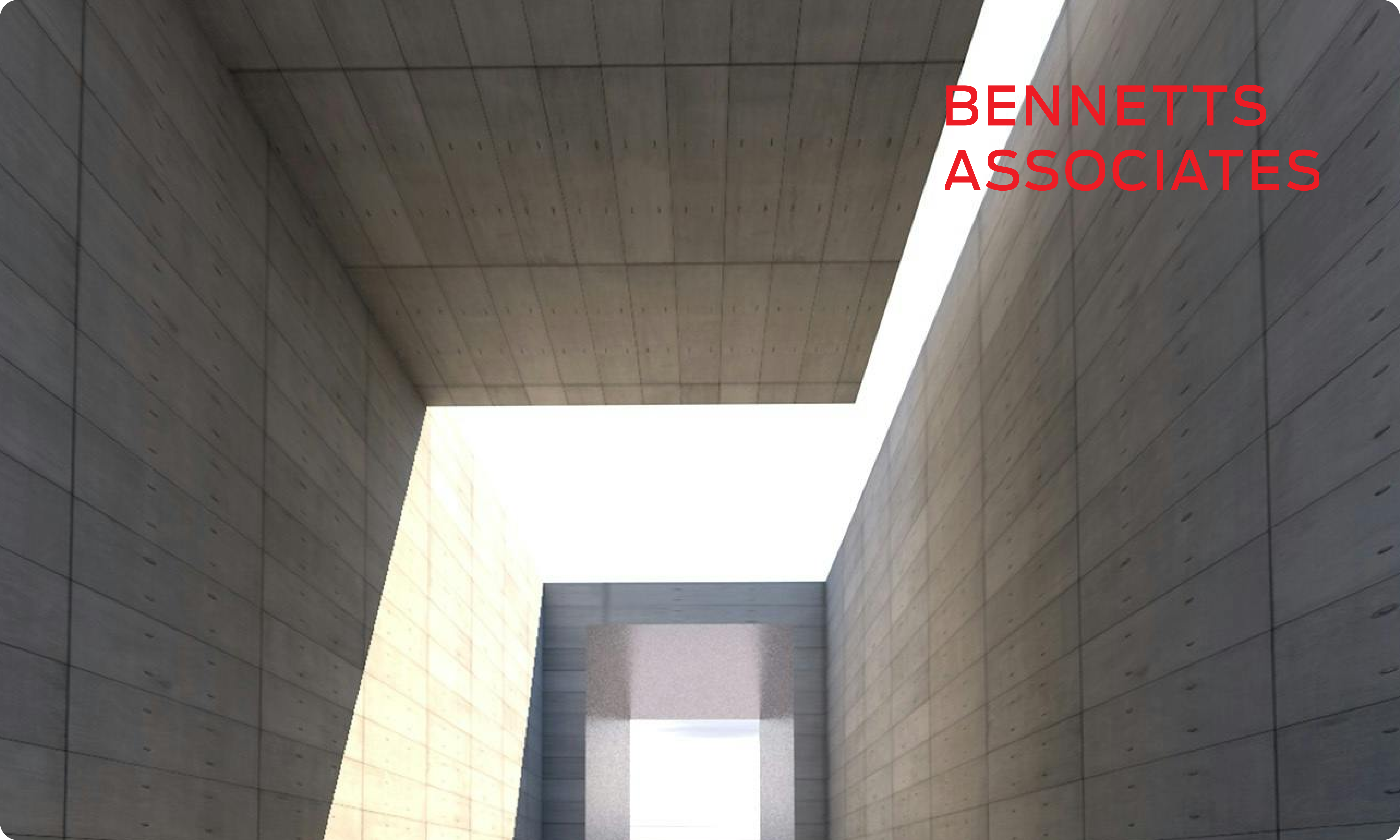
Laura Drury • Nov 28 2024
Aileen Carroll • Jul 03 2024
Laura Drury • Sep 02 2024
Asha Ramachandran • Aug 27 2025