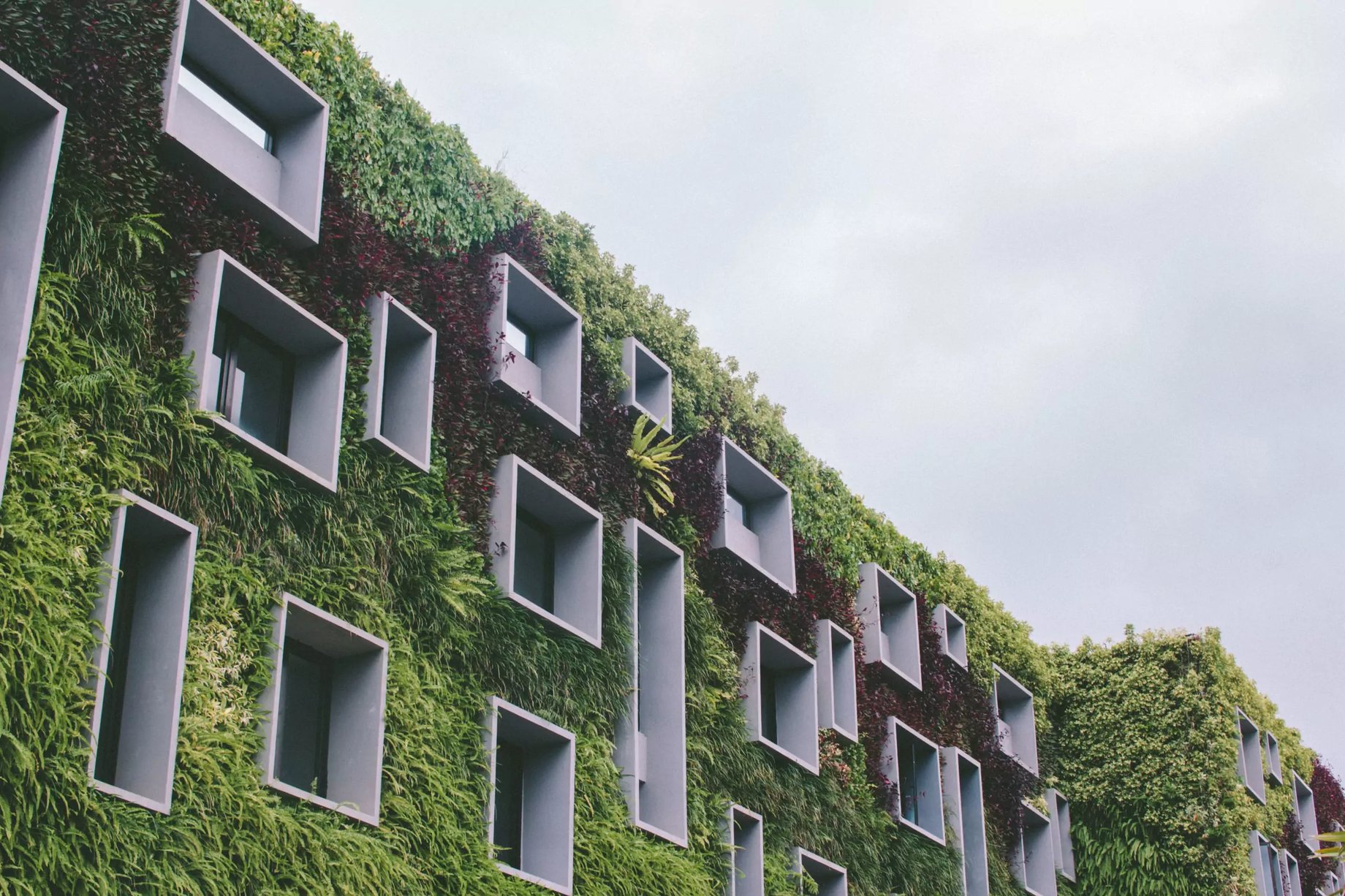
Ecodesign in Practice is a series of sustainable construction design solutions that can be applied at scale. The solutions are also integrated as data sources in One Click LCA for Buildings and Carbon Designer 3D. We publish an article and associated solutions once every six weeks. Enjoy reading!
The role of insulation in whole-life carbon optimization
The article highlights insulation’s vital role in optimizing whole-life carbon for buildings, explores different insulation types, emphasizes factors like thermal performance and safety when comparing insulation products, and discusses the decarbonization roadmap for insulation.
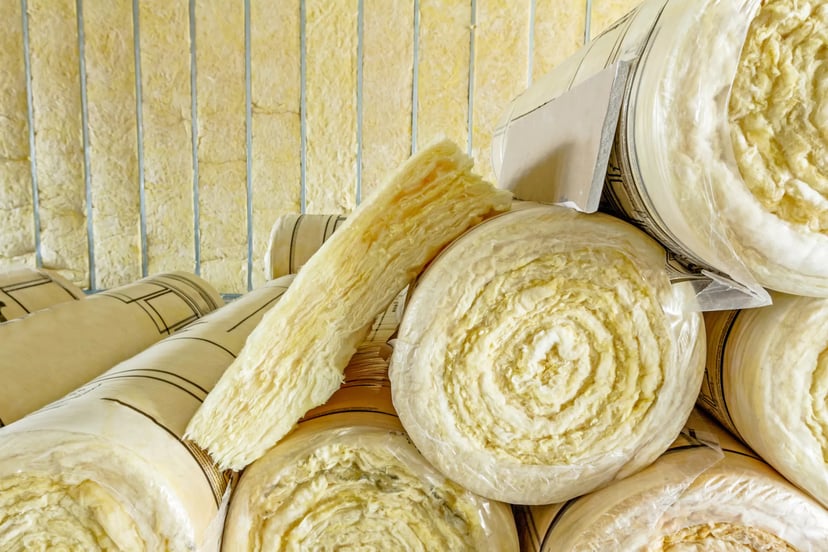
A quick guide for design teams and specifiers |
A checklist for reducing whole life carbon emissions from careful specification and sizing of insulation
|
Insulation plays a vital role in buildings by reducing heat loss or gain, ensuring comfortable indoor temperatures, improving energy efficiency, and reducing operational carbon emissions. It can be applied to various building components, including walls, floors, roofs, ceilings, and internal walls for sound insulation. The share of whole-life carbon emissions attributed to insulation depends on factors like building location and choices made for other impactful building parts.
In a UK baseline building compliant with energy regulations (Part L), insulation contributes approximately 8% of whole-life embodied carbon emissions, excluding operational energy. In locations with higher thermal insulation requirements, this share can be even higher.
The use of certain blowing agents, like Hydrofluorocarbons (HFCs), during insulation manufacturing can significantly increase the share of insulation in a building’s overall embodied carbon. In the European Union, blowing agents like Chlorofluorocarbon (CFCs) and Hydrochlorofluorocarbon (HCFCs) have been prohibited, while blowing agents like HFCs are gradually phased out.
In this article, we provide an overview of insulation types, important properties to consider when specifying them, and how to compare them to reduce whole-life carbon emissions.
The choice and thickness of insulation have a broader impact on life cycle carbon emissions, including operational energy efficiency. While thicker insulation reduces heat loss/gain, the additional amount of heat loss/gain that is prevented decreases as the insulation thickness is increased, as shown in LETI’s Climate Emergency Retrofit Guide. It is crucial to strike the right balance to maximize benefits and minimize overall emissions. Considering operational energy-related carbon emissions when specifying insulation type and thickness is key to minimizing whole-life cycle emissions.
Optimizing the amount of insulation
To optimise the thickness of insulation, the whole life carbon emissions related to insulation must be considered. This includes the embodied carbon of the insulation itself but also the operational carbon emissions from heating and cooling. The additional amount of thermal gain or loss that is prevented decreases as extra insulation thickness is added. The embodied carbon of insulation increases linearly as the thickness increases. This results in the insulation increasing the whole life carbon emissions after a certain thickness. The optimum point depends on:
- The insulation product, its carbon intensity, and thermal conductivity. Insulation products with higher embodied carbon will move the optimum towards smaller thicknesses. At the same time, insulations with lower thermal conductivity will allow for thicker insulation layers.
- The use of the building. Buildings that are not always or completely conditioned benefit less from the additional insulation in terms of operational carbon savings. Hence the embodied carbon of insulation may be higher than the energy savings.
- The location of the building. Buildings in locations where the difference between the external and internal temperature is higher throughout the year will benefit more from increased insulation thickness. This will allow additional insulation to be used until the operational savings are outweighed by the embodied carbon of the extra insulation.
- The technology and the energy source used for heating and cooling. In locations where the thermal energy supply has low carbon emissions, thick insulation may result in larger embodied carbon than operational carbon savings. Similarly, for locations where the electricity grid is low carbon when heating is produced via electricity (ensure that the decarbonization of the electricity grid is also taken into account).
The Trade-off: Operational Carbon Savings vs. Embodied of Additional Insulation
The following graph illustrates the balance between operational carbon savings and embodied carbon in different scenarios across Helsinki, London, and Rome. The study evaluated heat transfer in one m2 of the insulated brick wall with heating provided via air-source heat pumps. The insulation used was assumed to be EPS insulation with a thermal conductivity of 0.034 W/mK. The baseline design featured 5cm of insulation, assuming round-the-clock conditioning throughout the year. The insulation’s service life is aligned with the building’s lifespan of 50 years.
Scenario | Average annual temperature difference | Electricity grid carbon intensity (kgCO2e/kWh) |
Helsinki, Finland | 15°C | 0.16 |
London, UK | 7.75ºC | 0.14 |
Rome, Italy | 5.6ºC | 0.49 |
The following graphs determine the optimum insulation level for each country (Finland, UK, and Italy) The electricity grid carbon intensity considered in this study represents the current carbon emissions per kWh in each country. As the electricity grid is set to decarbonize within the next few decades in all three countries, the insulation thickness should be specified well below the optimum point shown in these graphs. Alternatively, if data is available, an average carbon intensity factor may be taken into account in similar studies that represent average annual emissions from today until 2050.
What are the different types of insulation?
Insulation materials can be categorised into the following main types based on the origin of materials:
- Mineral (rock/glass) insulation
- Synthetic (plastic-based) insulation
- Natural (organic) insulation
1. Mineral (Rock/Glass) Insulation
Mineral insulations are made of mineral materials like stone (e.g. basalt and dolomite), glass, and other materials.
The most used mineral insulations are:
Stone wool
Stone wool is created by melting stones such as basalt and dolomite, along with slag, at temperatures around 1400ºC. The molten mixture is then spun through tiny holes in a machine to form mineral fibres. These fibres are combined with a binder, shaped into mats and boards of different thicknesses, and heated again to set the binder.
Thermal conductivity: 0.03 to 0.04 W/(mK)
Applications: Versatile insulation material but most typically used for external wall insulation and cold roof insulation.
Glass wool
Glass wool is primarily composed of silica sand, limestone, and recycled glass. These materials are combined and melted at temperatures of approximately 1500°C. Like stone wool, the molten mixture is then processed through a spinning machine, resulting in the formation of glass fibres through tiny holes.
Thermal conductivity: 0.035 to 0.045 W/(mK)
Applications: Similar to stone wool
Insulating plaster
Insulating plaster is made from materials such as clay, and lime. It can be applied to solid walls like traditional plaster. Its low thermal conductivity enhances the thermal insulation of the element. Additionally, insulating plaster helps regulate humidity when used as a final finish material.
Thermal conductivity: Typically 0.2 W/(mK)
Applications: Internal finish of external and internal solid walls
Insulating blocks
In addition to traditional insulation materials, certain building blocks can serve as both core wall materials and insulation due to their low thermal conductivity. Examples include autoclaved aerated concrete blocks, also known as Ytong, vertically perforated bricks, and variations where the brick holes are filled with expanded polystyrene to reduce the thermal conductivity further.
Thermal conductivity: autoclaved aerated concrete blocks- 0.14 W/(mK)
Vertically perforated bricks-0.21 W/(mK),
variations with brick holes filled with expanded polystyrene-0.13 W/(mK).
Applications: Solid external walls
Cellular glass
2. Synthetic/plastic-based insulation
Synthetic insulation products are made from petrochemical materials and expanded with blowing agents during manufacturing. Despite international agreements regulating high GWP blowing agents, they are still used in some countries, leading to a significant variation in the embodied carbon of these products.
The most commonly used synthetic insulations are:
Expanded Polystyrene (EPS)
EPS insulation is produced by heating polystyrene beads mixed with a blowing agent, that causes them to expand. The expanded beads are then cooled, stabilised, and placed in moulds where they undergo further expansion when heated with steam. This process fuses the beads together, creating a closed cell structure.
Thermal conductivity: 0.03 -0.04 W/mK.
Applications: typically applied as external insulation to walls and structural elements, ground floor insulation and flat accessible roofs.
Extruded Polystyrene (XPS)
XPS insulation is made of polystyrene pellets heated to their melting point. During extrusion, a blowing agent is added to the molten polystyrene, causing it to vaporise and expand, creating a closed cell structure. After shaping, the extruded polystyrene is rapidly cooled using cool air and water.
Thermal conductivity:0.03 -0.035 W/mK.
Applications: XPS is being used for similar applications as EPS.
Polyurethane foam (PUR)
PUR is a foam insulation created through a chemical reaction between petroleum-derived polyol, isocyanate, and a blowing agent. When combined, these components undergo polymerization, forming polyurethane foam and expanding as the blowing agent releases carbon dioxide.
Thermal conductivity: 0.02 -0.023 W/mK.
Applications: PUR can be applied as rigid boards to external walls and roofs or sprayed into cavity walls during renovations. PUR is also typical for Structural Insulated Panels (SIPs).
Polyisocyanurate foam (PIR)
PIR insulation is manufactured in a similar way as PUR but with a higher proportion of isocyanate. This results in lower thermal conductivity and better fire resistance.
Thermal conductivity: 0.018 – 0.022 W/mK.
Applications: Similar to PUR
Phenolic insulation
Phenolic insulation is made by mixing phenolic resin (made by mixing phenol and formaldehyde) with a blowing agent under heat and pressure to activate the blowing agent. The reaction generates carbon dioxide which creates the cellular structure of the phenolic foam.
Thermal conductivity: 0.018 -0.022 W/mK
Applications: Similar to EPS and XPS
3. Natural (organic) insulation
Natural insulations are insulation products that use natural, bio-based, raw materials. Such raw materials can be plant-based or at lesser extent animal based.
The most commonly used natural (organic) insulations are:
Wood fibre
Wood fibre is manufactured from wood, typically wood waste (chips and shavings). The shavings are mixed with water and latex or paraffine (as binder). The pulp is then mechanically pressed and dried to create the insulating boards. The biggest embodied impacts are due to the drying process, which requires energy in the form of gas or electricity.
Thermal conductivity: 0.038 W/mK at 50 kg/m3 . Applications: It is a relatively flexible and weather-resistant insulation that can be used for sheathing and sarking, external walls, or floor insulation between the structural slab and screed.
Cellulose Insulation
Cellulose insulation is made of paper fibres, mainly recycled. Paper is cut into pieces and then fiberized.
Thermal conductivity: 0.04 W/mK
Applications: It can be applied as dry loose fill in cavities or mixed with adhesives and water to achieve a more stable insulation with no settling over time.
Hemp
Hemp insulation is manufactured using mainly hemp fibres, polyester, and fire retardants. The insulation boards are formed through mechanical compression and heating. The boards are then cut to shape. Like wood fibre insulation, the biggest embodied impacts are due to the heating process, which requires energy in the form of gas or electricity.
Thermal conductivity: 0.039 W/mK
Applications: Hemp insulation is typically used as roof insulation, ceiling, and façade insulation
Straw bale
Straw bale insulation is made from compacted straw bales. Straws are typically derived from wheat, rice, barley, and other grain crops.
Thermal conductivity: approximately 0.06 W/mK.
Applications: Straw bale insulation is mostly used in external walls typically in timber buildings
Wool
Wool insulation is made by combining recycled wool from textiles, virgin wool, and a mixture of recycled and new polyester. The manufacturing process includes sorting and blending the wool fibers, washing, drying, combing, layering, and bonding.
Thermal conductivity: 0.041 W/mK
Applications: Wool insulation is typically used to fill hollow spaces in roofs, walls, and floors
Making the right insulation choice
There is an abundance of different insulation products in the market with different densities, different insulation performance, made by different manufacturers who have different manufacturing processes and use different primary energy sources. This does not allow for a generally valid conclusion on what insulation type and amount results in the lowest carbon emissions. The four general principles that should be followed when looking for the best-performing insulation for your project are:
- Exclude the insulation solutions with the worst blowing agents
- Optimise insulation level (above minimum required)
- Ensuring the thermal performance and functional equivalence of all compared insulations
1. Exclude the insulation solutions with the worst blowing agents
Ensure that your insulation is not among the most carbon-intensive ones in the market, make sure that it has not used high GWP blowing agents like CFCs, HCFCs, and HFCs. Such products typically do not have EPDs due to the EPDs daylighting their disproportionately high GWP impact.
2. Optimize insulation level
Optimize the insulation thickness by assessing and comparing the operational savings vs. the embodied carbon from any additional insulation thickness, as explained above. This will help you decide if the insulation should be increased above the minimum required.
3. Ensuring thermal and functional equivalence
When comparing insulation products, thermal performance equivalence must be ensured. The u/R-value of the insulated element must be the same for each insulation option being compared.
4. Ensuring other functional equivalence
The overall function of the building must also be considered when comparing different insulation options. This includes basics, such as acoustics and fire safety, but also total layer thickness. A lower-carbon insulation may not be the best option if it has to be a lot thicker because it will result in thicker wall and floor elements.
How to compare insulation products in practice?
The simplest and fastest way to compare insulation products is to define the insulation thickness for each of them in order to achieve the same thermal resistance (R-value) and compare their embodied carbon on an area basis (Impacts per m2 or ft2 of insulation). However, if the thickness of a lower embodied carbon option is considerably higher (e.g. 10-15%), a full element or whole building assessment must be undertaken. This is to include the additional embodied carbon from the elements that support the insulation and the increased wall or floor size to accommodate the additional insulation thickness.
Data to help you choose the best-performing insulation
One Click LCA’s database currently contains 4781 insulation datapoints. This number continues to grow as more manufacturers provide EPDs for their products and as One Click LCA develops more generic materials. These datapoints can be categorised as follows:
- 3836 manufacturer-specific EPDs
- 945 generic insulation datapoints (either generic EPDs or generic materials from industry and regulatory databases)
- 74 generic insulation datapoints developed and maintained by One Click LCA. These datapoints are localised to the manufacturing conditions of any country across the world. This allows One Click LCA users to complete their assessments even when manufacturer-specific EPDs are not available in their region.
One Click LCA generic datapoints include the following insulations at various densities and thermal conductivity (lambda values).
Mineral insulation | Synthetic insulation | Natural (organic) insulation |
Rock wool insulation | EPS | Wood fibre insulation |
Cellular glass insulation | PIR | Cellulose insulation |
Glass wool insulation | PUR | Hemp fibre insulation batts |
XPS | Hemp fibre loose insulation | |
Rice straw bale | ||
Wood fibre insulation | ||
Seed and mulch | ||
Hemp straw |
Where can I find EPDs for insulation products?
To make an informed decision regarding insulation for your project, it is crucial to have access to key information such as the product’s environmental impacts, lambda value, density, and product description to ensure suitability for your specific requirements. This information is readily available in manufacturers’ Environmental Product Declarations (EPDs), which are extensively represented in the One Click LCA database. Below are some selected manufacturers that have created EPDs for their insulation products.
- Kingspan Insulated Panels (UK and various others)
- Isover (various locations)
- Knauf (various locations)
- IKO Insulations BV (NL)
- Konto Oy (FI)
- Amorim Cork Insulation (PT)
What does the decarbonization roadmap look like for insulation?
The carbon emissions associated with most insulation types primarily stem from the energy source used during manufacturing, particularly in the heating or melting processes. Additionally, synthetic insulations may contribute to emissions through the use of blowing agents. In the past, insulation manufacturers commonly utilised CFC and HCFC blowing agents, but regulations have significantly restricted their use due to concerns about Ozone Depletion and Global Warming.
Furthermore, restrictions are now being placed on HFC blowing agents in many countries. However, alternative blowing agents with lower GWP, such as HFOs, CO2, butane, and pentane, have emerged, offering the potential for even further reductions in related carbon emissions in the future.
The emissions related to energy usage depend on the energy mix employed by manufacturers. Presently, many manufacturers rely on coal and other fossil fuels for thermal processes, such as high-temperature melting reaching approximately 1500°C. However, by transitioning from fossil fuels to electricity, combined with the adoption of on-site renewable energy sources and the broader decarbonisation of the electricity grid, it is expected that carbon emissions can be minimised.
Knauf is currently investigating the use of biogas and hydrogen and is planning to reduce its carbon footprint with these technologies in the next two decades. Rockwool uses entirely electricity in their new factory in Qingyuan, China, and has switched from coal to natural gas in their Mississippi factory in the USA.
Visualizations
Carbon Experts Newsletter
Industry news & insights — straight to your inbox
Want to learn more?
Marios Tsikos • Feb 08 2024
Asha Ramachandran • Sep 01 2023
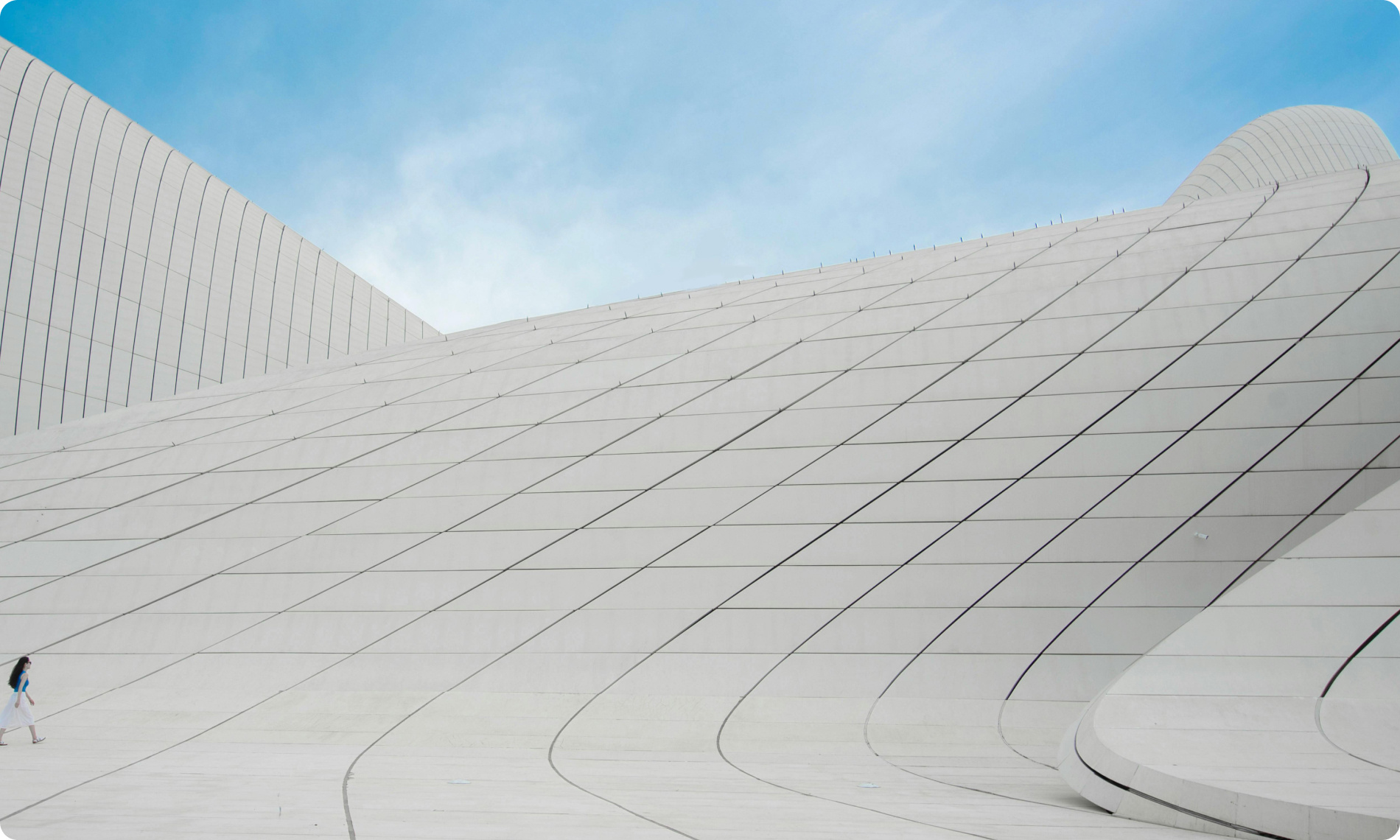
Justyna Michalik-Minken • Apr 14 2025
Melina Zacharia • Feb 20 2024