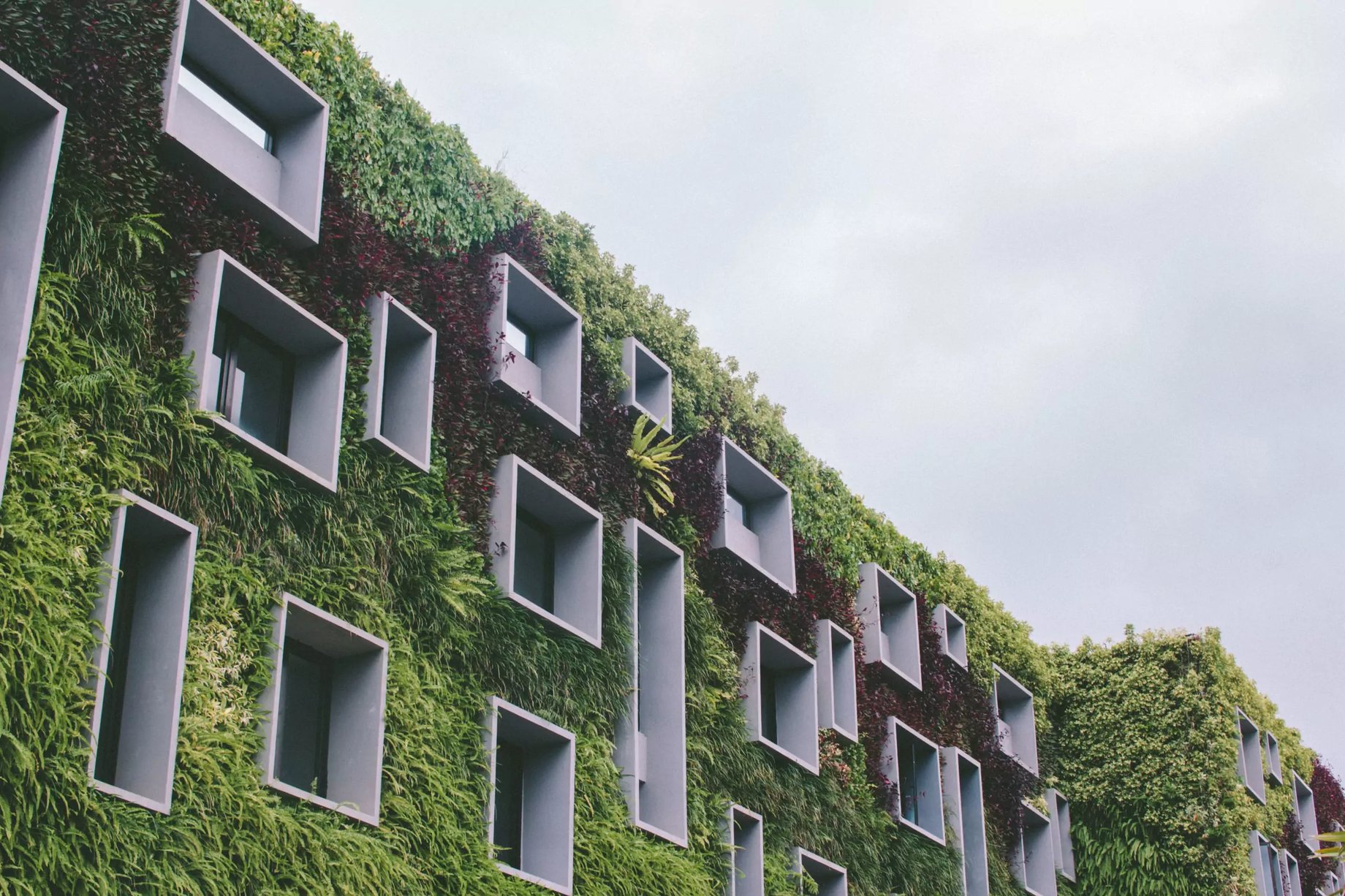
Ecodesign in Practice is a series of sustainable construction design solutions that can be applied at scale. The solutions are also integrated as data sources in One Click LCA for Buildings and Carbon Designer 3D. We publish an article and associated solutions once every six weeks.
Structural timber: how to make it work for your project

Why structural timber?
Structural timber has lower embodied carbon, as its processing does not require high temperatures or significant quantities of fossil energy sources. However, the caveat is that if the timber is harvested from unsustainably managed forest or if the logging is a final clearing (i.e. land will not be replanted as a forest after logging), the resulting land use carbon emissions switch the picture completely. This article therefore considers timber from sustainably managed forestries. Such timber sources can be identified for example by PEFC or FSC labels.
Types of structural timber
Structural timber refers to building elements made of wood that are load-bearing and can be used in the construction of buildings and other structures.
Structural timber can be used for columns, beams, walls, and slabs. It is typically made of softwood species like pine, spruce, and fir among others.
Commonly used structural timber products are:
- Cross Laminated Timber (CLT)
- Glued Laminated Timber (Glulam)
- Laminated Veneer Lumber (LVL)
Stick frame timber is only suitable for low-rise buildings but is an even more material- and carbon-efficient timber construction method.
Structural timber has lower embodied carbon compared to steel and concrete if sourced from sustainably managed forestries.
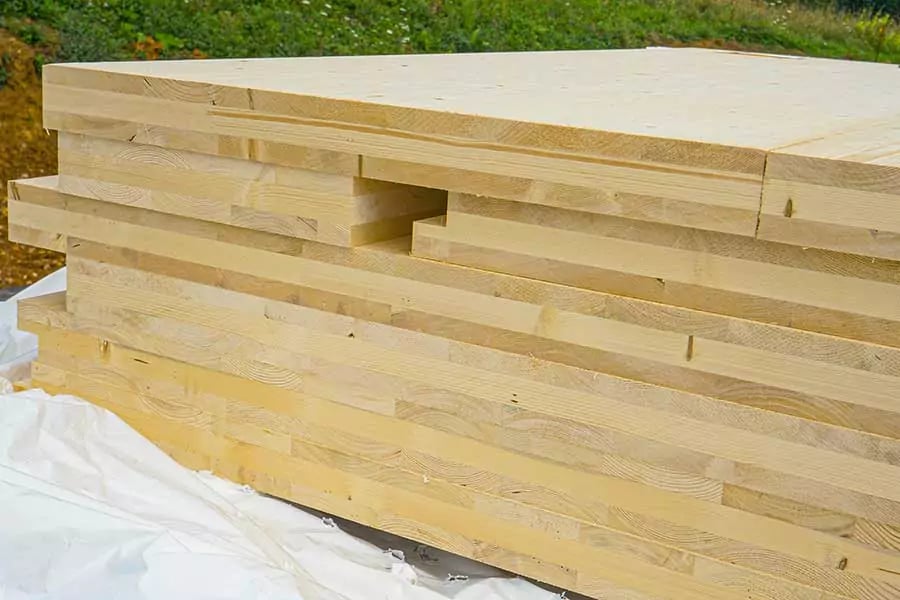
- CLT is a structural timber product made from layers of lumber boards stacked in alternating perpendicular directions glued together to form a solid panel.
- These panels can be fabricated in different sizes and thicknesses according to the specific needs of a construction project.
- CLT is typically used for slabs, load-bearing, and non-load-bearing walls in a building.
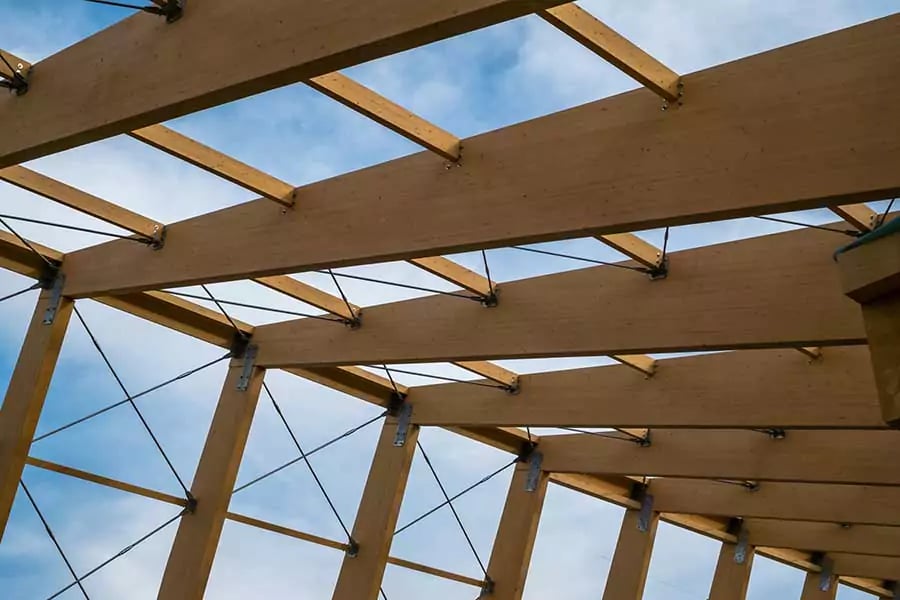
- Glued Laminated Timber (Glulam) is a linear structural timber product made from wood laminations bonded together using a durable and moisture resistant adhesive.
- The laminations are bonded in such a way that the wood grains run in parallel with the element’s longitudinal axis.
- Glulam is typically used for column and beam elements in a building.
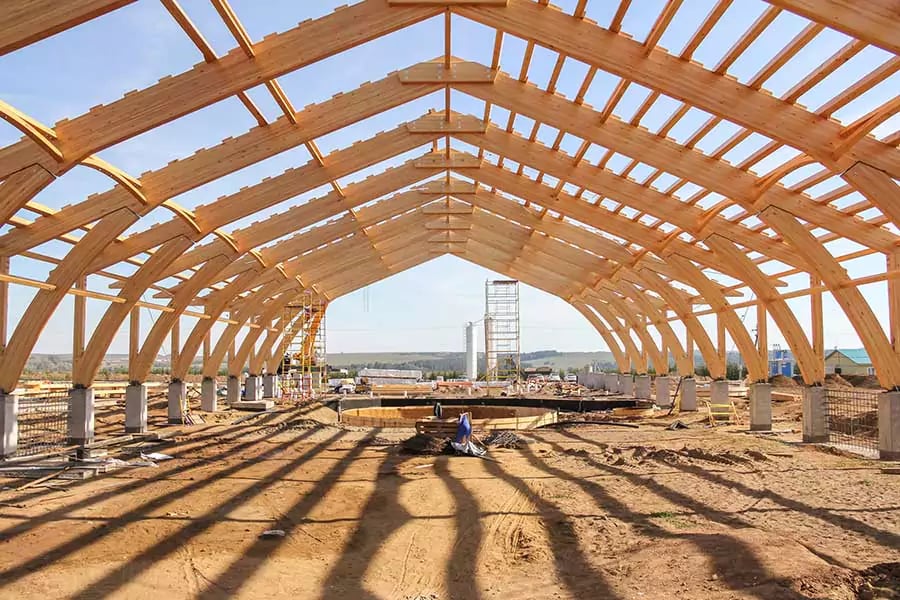
- Laminated Veneer Lumber (LVL) is an engineered wood product manufactured from rotary peeled veneers, assembled with parallel grain orientation and bonded with a structural adhesive.
- LVL can be used for framing and is suitable for longer spans for example in large roof and floor structures.
Commonly used structural timber products are Cross Laminated Timber (CLT), Glued Laminated Timber (Glulam), and Laminated Veneer Lumber (LVL)
Biogenic carbon storage
Biogenic carbon in the context of structural timber refers to the carbon that is sequestered and stored in trees through the process of photosynthesis. This carbon is absorbed from the atmosphere and transformed into the trees’ biomass. When the tree is cut and processed into a structural timber product, this carbon remains stored for decades until the product is incinerated or decomposes.
It is a common conception that timber is a more climate-friendly material because it stores carbon, and this results in negative embodied carbon. Unfortunately, as is often the case, the full picture is not quite so simple. The vast majority of the buildings built today are not designed or delivered in a manner to allow for the reuse of the timber structures after the end of the building’s life. This results, in most cases, in the timber being incinerated after deconstruction or demolition, which releases the carbon back into the atmosphere. While this does delay the emission of the biogenic carbon emissions stored in the buildings by several decades, it clearly cannot be considered as negative embodied carbon.
Since different users may wish to account for this in different ways, One Click LCA’s Net Zero Tool allows the user to choose whether the biogenic carbon storage is accounted for as negative carbon emission. It’s worth noting that any eventual incineration of the timber to produce energy at end of life can also have positive impacts. By generating energy without using conventional fossil-fuel reliant energy production processes there is an overall reduction in fossil fuel use. In an LCA these benefits are reported in module D, which quantifies the impacts after the end of life of the building. More information about biogenic carbon and carbon sequestration can be found in this article from the Institution of Structural Engineers: Timber & Carbon Sequestration.
Biogenic carbon refers to the carbon sequestered and stored in trees through the process of photosynthesis and One Click LCA’s Net Zero Tool helps you with it.
Comparing timber solutions in practice and data to help you do that
When comparing timber structural solutions with concrete or steel it is not appropriate to do a direct mass- or volume-based comparison as each material has different physical and durability properties, such as compressive and tensile strength, water- and corrosion- resistance, and so on.
The best way to compare structural materials and quantify their impacts is by creating different design options and comparing the carbon impact of the whole structural system at a building level.
You need to make decisions about structural solutions very early on in your project. Often during these phases, very little has been agreed about the project. Luckily, One Click LCA provides customers with several solutions and data to enable early-phase design comparisons, including: Carbon Designer 3D and generic material datapoints.
One Click LCA’s early design optimisation tool Carbon Designer 3D can now create and compare early stage CLT and Glulam frame building designs in Europe, the USA and Canada and the Middle East and Africa.
One Click LCA’s early design optimisation tool Carbon Designer 3D can now create and compare early stage CLT and Glulam frame building designs in Europe, the USA and Canada and the Middle East and Africa.
- Cross laminated timber (CLT)
- Glue laminated timber (Glulam)
- Laminated Veneer Lumber (LVL)
- 62 other generic CLT/Glulam/LVL material datapoints from open generic material databases and regulatory databases
One Click LCA database integrates virtually all EPDs that are available in the market. The One Click LCA database currently includes 174 EPDs for CLT, Glulam and LVL products.
When to use generic data
In the event that an EPD has not been developed for a structural timber product or if the product to be used is currently unknown, then, the generic material datapoints mentioned above will help you complete your assessment. These datapoints like all other One Click LCA generic datapoints are localized for any country and they represent average materials for the performance criteria defined.
The One Click LCA database currently includes 174 EPDs for CLT, Glulam, and LVL products and 62 other generic CLT/Glulam/LVL material datapoints.
Carbon Designer 3D structural timber templates
During the early design stages, the design team will typically conduct an options appraisal where different design options are compared with each other with the aim of identifying the lowest embodied carbon option or quantifying the benefits of an option against others. While this exercise is most beneficial at the early stages, the lack of design documentation is a barrier. To overcome this barrier, design teams can use One Click LCA’s Carbon Designer 3D, an early design stage tool that allows its users to estimate material quantities and environmental impacts.
- The three scenarios assessed include a CLT structure, a concrete, and a steel one.
- The assessment includes the foundations, structure, envelope, internal walls, and finishes.
- The scope includes modules A1-A3, A4, A5, B4 and C2-C4
- Slabs and frame are the main points of differentiation. In all three scenarios, these elements are functionally equivalent i.e. fire safety, load capacity, and acoustics.
- 240mm thick CLT slabs are used in the CLT option, 150mm concrete slabs in the concrete option, and 150mm composite metal decks in the steel option.
- Screed topping, acoustic insulation, and plasterboard ceiling are included in the CLT slabs for functional equivalence. All CLT walls are assumed to be covered with acoustic insulation and gypsum boards.
- For internal walls 175 mm thick CLT panels were used and 120 mm CLT panels for external walls. For the concrete option C30/37 with 10% GGBS has been assumed. While 60% recycled content is assumed for the steel option.
Contribution of building material
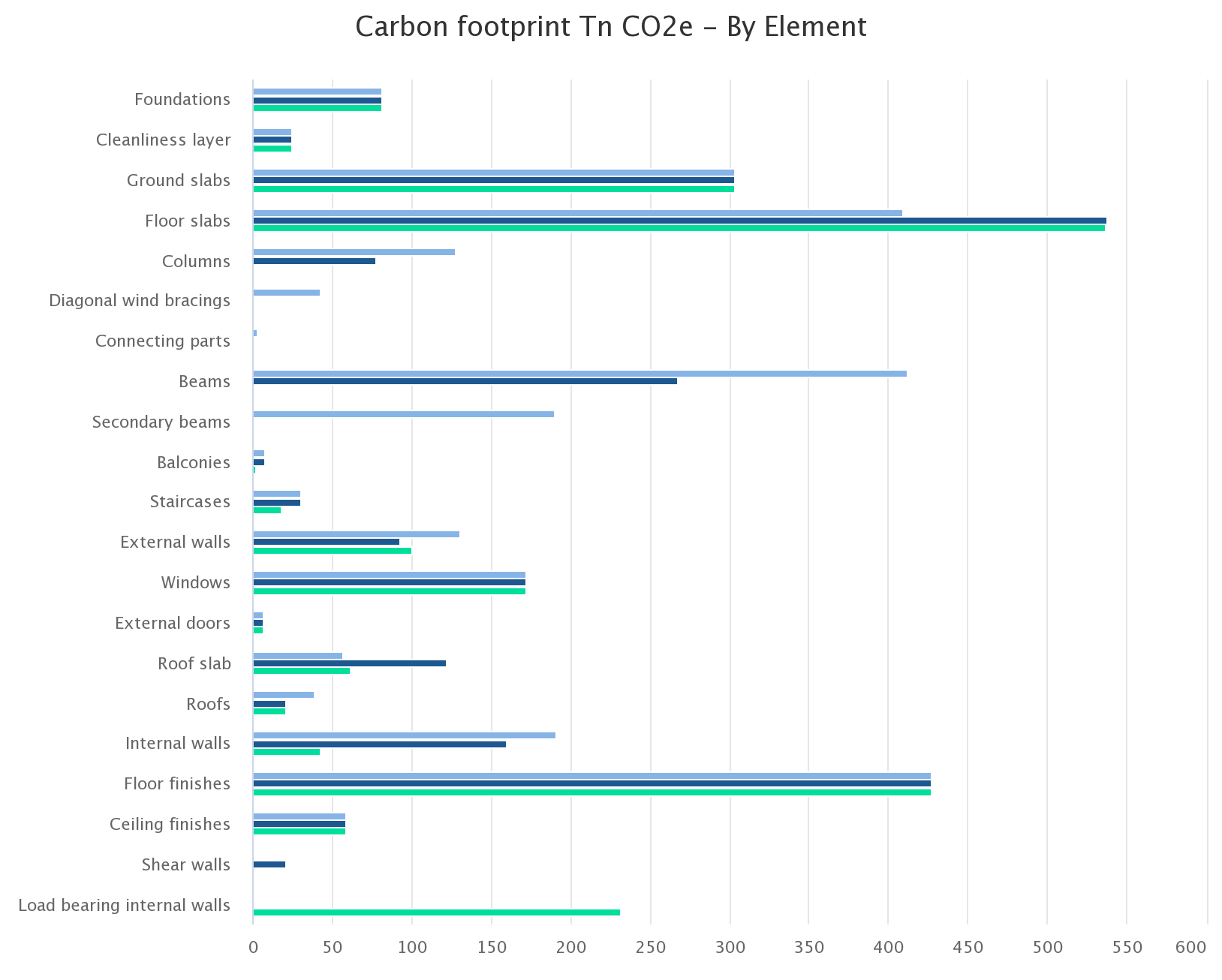
Contribution of building parts
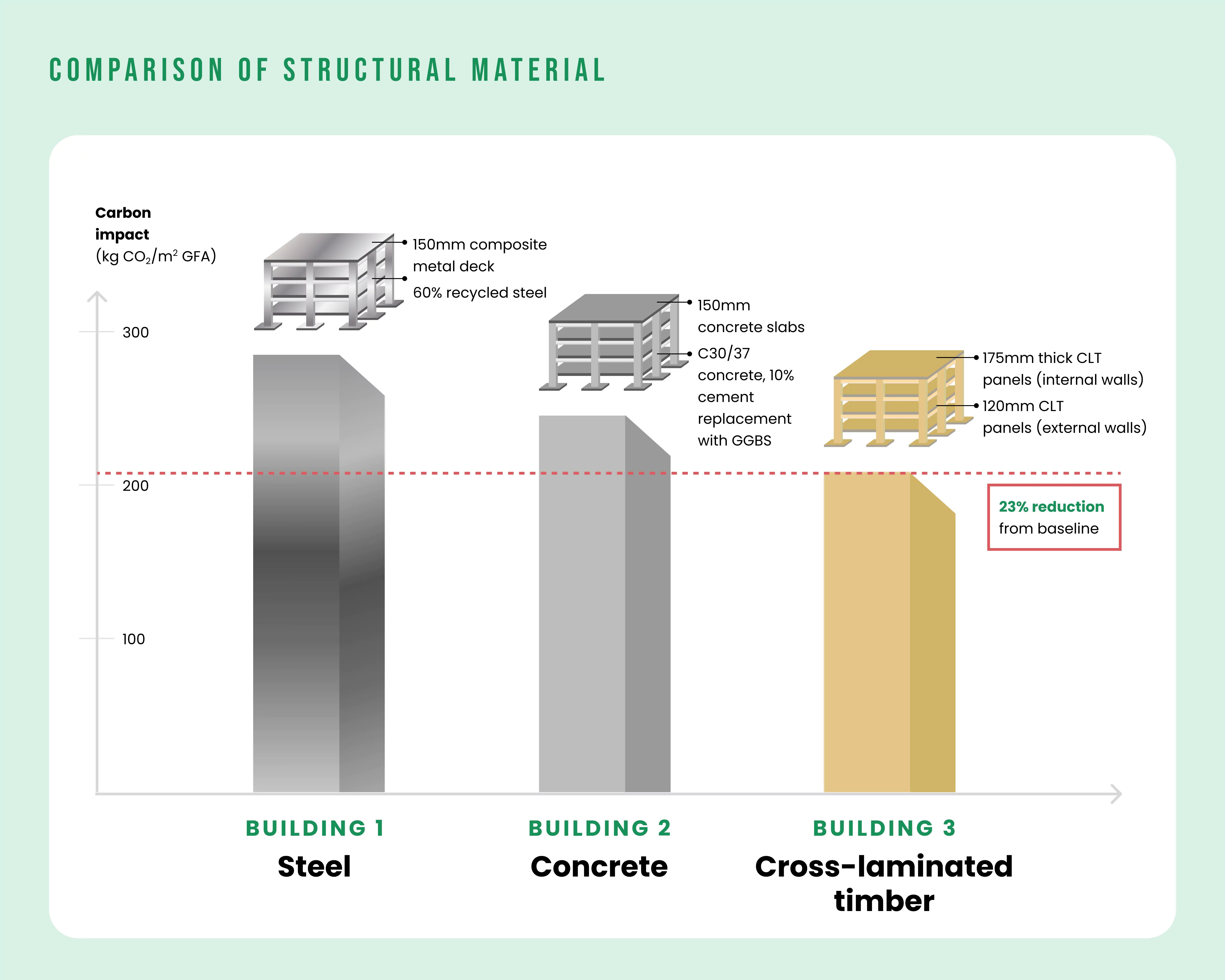
Structural timber can result in a 23% reduction of GWP impacts compared to a baseline structure made of steel or 14% compared to a concrete structure at a whole-building level.
Module D benefits and impacts of timber
Module D have very high uncertainty since the energy grid will very likely be fossil-free in the future. Arguably, it is also secondary from the point of view of the present climate crisis, where cutting emissions immediately is of the highest value. Due to this, any replacement scenarios considering fossil fuels or substituting fossil-energy based steel production are likely wrong. In One Click LCA, to change the end-of-life energy substitution scenario to the one you consider most plausible after the end of the building’s life-cycle, use the project’s LCA Parameters, and to change end-of-life scenarios for any of the materials, use the relevant modeling feature in the tool. These functionalities are not available in tools where the standard or methodology mandates the calculation method.
More information about One Click LCA’s LCA Parameters can be found in this article.
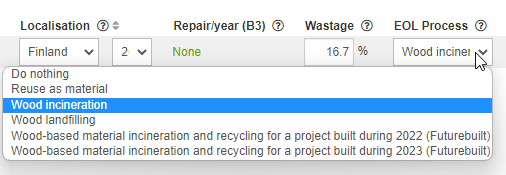
Does this work for your project? Your call!
One Click LCA promotes design for performance, that compares the costs, carbon and time to build among the available solutions that meet the functional requirements.
While timber construction has significant environmental benefits, advantages for seismic regions, and it provides a lighter building frame overall, it also has some limitations to consider.
- Fire resistance: For fire safety purposes, timber buildings require additional gypsum boards to act as fire retardants, which in turn increase the mass and carbon impact of the building. Local fire codes usually limit the maximum height of the timber buildings.
- Acoustics: It strongly correlates with mass. Timber floors typically need a ready-mix concrete layer to increase floor mass and acoustic performance to ensure step noise is not disturbing. This can be remedied for example with a heavy, yet low-carbon material such as sand or gravel on top of floors prior the leveling screed.
- Moisture resistance: Depending on your location and solutions, timber buildings may require protection from the elements in the construction phase. This increases construction costs.
- Ensuring sustainable forestry management for the timber supply: Most practicable way to ensure this is to require PEFC or FSC certification.
- Availability: Sustainable forestry is not a common practice worldwide, and importing timber over significant distances reduces potential carbon gains.
More and more companies are providing structural timber solutions. They can be found for example via national timber construction associations. Below are just some of the timber construction firms that provide or are working to provide third-party verified EPDs for their products:
Europe
- CrossLam Kuhmo
- Stora Enso
- AS Barrus
United States
New Zealand
Checklist: How to reduce embodied carbon when working with structural timber
Carbon Experts Newsletter
Industry news & insights — straight to your inbox
Want to learn more?
Panu Pasanen • Jan 19 2023
Asha Ramachandran • Sep 01 2023
Marios Tsikos • Feb 14 2024
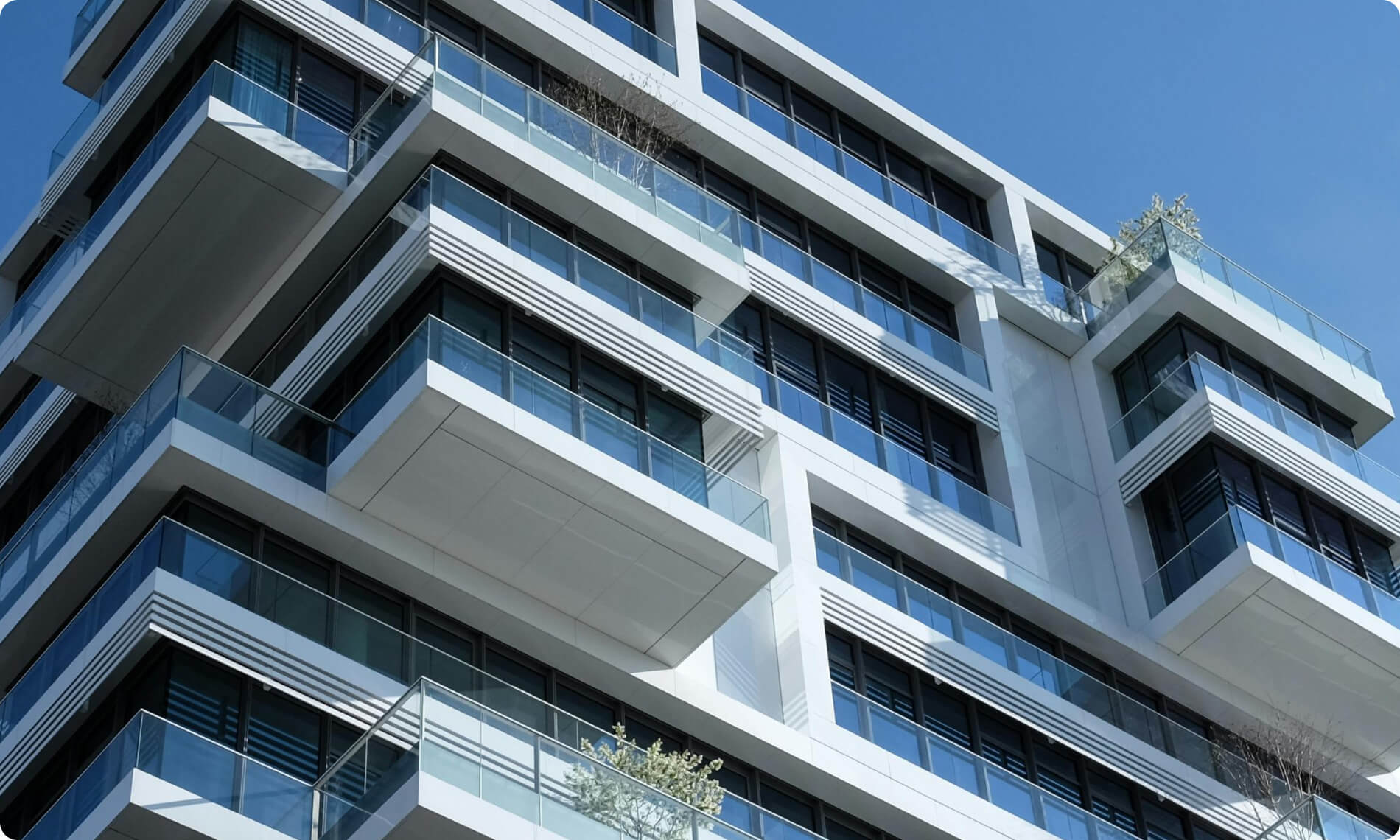
Laura Drury • Jul 24 2025