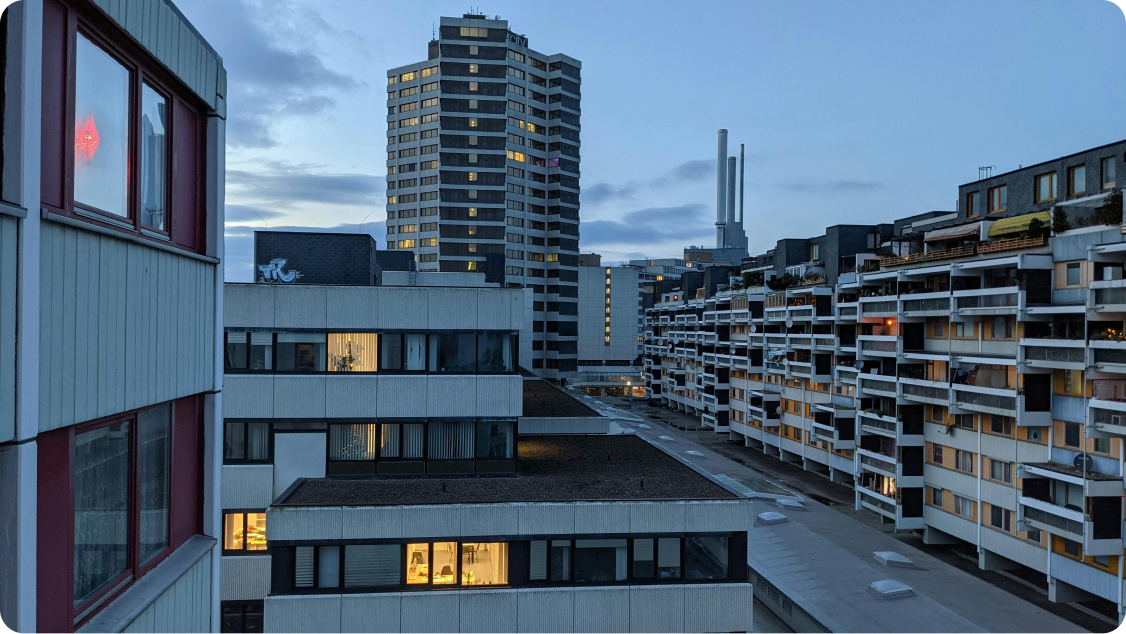
Circular construction requires the implementation of sustainable concrete solutions that promote material reuse, recycling, and reduced environmental impact. How you can leverage One Click LCA to find and compare concrete mixes?
The road to circular concrete
The vast majority of concrete’s embodied carbon is released during the production stage (A1-A3). Even when alternative binders are used there still remains a significant A1-A3 impact. A great way to reduce these impacts in the future is to reduce the need for new concrete to be produced. As the demand for concrete is not expected to reduce in the next few decades, the only way to make this happen is to use concrete in elements that can be reused in the future.
The most likely end-of-life scenario currently for concrete is to be crushed into aggregates. However these aggregates cannot be reused indefinitely or at high rates in structural elements because of the monolithic structure of in situ concrete which makes it impossible to be disassembled and reused. Precast concrete elements when designed properly can allow for future disassembly and reuse. The key in enabling building elements like concrete columns, beams and panels to be reused is the careful design and reversible implementation of the connections. 3XN Architects are well known for their research in low-carbon and circular materials. In their report Building a Circular Future, they propose reversible connections for elements made of concrete among others.
The role of specifiers in low-carbon concrete
Concrete specifications are based on national standards that define the concrete grade and water to cement ratio to be used based on climate and exposure zones. Structural engineers may go a step further from national standards and specify performance-based requirements for concrete mixes. A performance-based specification will define the durability requirements, for example resistance to carbonation, maximum acceptable shrinkage of concrete, compressive strength when concrete is fully cured, and minimum early compressive strength in a set period of time as required for the continuation of construction. Early compressive strength should ideally be evaluated in longer periods than typically done with Portland cement mix to allow for the use of alternative binders to cement. Maximum embodied carbon may be specified for the concrete grade specified as above. The embodied carbon limits should be based on local availability and should also consider the concrete production related impacts, transportation to the site and site wastage.
The role of contractors in low-carbon concrete
Contractors should aim to procure low carbon concrete as per the low carbon concrete specification. If the specification is not performance-based, they should procure concrete from manufacturers with documented low embodied carbon for the required concrete grade through the use and comparison of EPDs (environmental product declarations) where available. Where EPDs might not be available, concrete mixes with maximized use of alternative binders should be preferred. Pressure should be applied to local suppliers to document their low carbon concrete mixes with EPDs. During construction, a considerable embodied carbon reduction can be achieved by minimizing the concrete wastage on site or the use of precast concrete elements where possible.
How to compare concrete mixes & how to model low-carbon concrete in One Click LCA
The One Click LCA database has tens of thousands of data points for ready-mix concrete of which approximately 6500 are generic data points representing typical production processes for various types of concrete. Many of these generic data points come from industry-average EPDs like the ones produced by NRMCA in the USA and Canada. There are plenty of other generic data points coming from regulatory databases from European governments. Additionally, One Click LCA provides its generic data points for different types of ready-mix concrete worldwide.
The list below summarizes the ready-mix generic data points that are available in the One Click LCA database to help you model your concrete embodied carbon at early stages and when a concrete plant-specific EPD is not available:
- Industry average EPDs from manufacturer associations (e.g. NRMCA)
- One Click LCA generic data points for Portland cement mixes and concrete grades ranging from C12/15 (1700/2200 PSI) to C60/75(8700/10900 PSI)
- One Click LCA generic data points for concrete grades as above with cement substituted with PFA at a range from 10% to 50%.
- One Click LCA generic data points for concrete grades as above with cement substituted with GGBS at a range from 10% to 75%.
You can also create YOUR concrete specification using the following datasets:
- Portland cement
- Ground Granulated Blast Furnace Slag
- Pulverised Fly Ash
- Silica Fume
- Metakaolin
- Standardized cement types like CEM I, CEM II, CEM III, and CEM IV
- Virgin and recycled concrete aggregates at various densities
For hempcrete-based solutions, you can use the One Click LCA generic data points for hempcrete, shotcrete with hempcrete and hempcrete masonry units. The One Click LCA database is continuously enriched with more generic datapoints to cover concrete mixes with alternative binders at different percentages. If you are considering a concrete mix with an alternative binder at a percentage at which there is no ready-to-use datapoint, you can model your own concrete mix by using datapoints for Portland cement, other cement types, alternative binders, sand and aggregate datapoints as listed above. One Click LCA enables you to save these alternative concrete mixes as private constructions, store them as datasets in your library and reuse them as single datasets in your building LCAs in the future.
Find out more about how to create private datasets and private constructions with One Click LCA.
How to compare different concrete mixes
A quick and simple way to compare different concrete mixes using One Click LCA is to add the data points of interest to the “compare data” feature. This will automatically generate a graph showing the carbon emissions per life cycle module for each of the compared mixes for the required functional unit. The feature is available for both generic data points and manufacturer specific EPDs and can be used for any material type.
Find out more about how to use the Advanced Material Comparison feature.
Sustainable concrete reinforcement
Concrete, especially in buildings, will typically be used together with steel reinforcement. Reinforcement is necessary in order to allow concrete elements to carry tensile forces which otherwise would not be possible due to concrete’s low tensile strength. Depending on the region, the reinforcement rate and the recycled content of the steel reinforcement bars, reinforcement can be responsible for up to 50% of the reinforced concrete’s embodied carbon. (100% Portland cement mix with 60% recycled rebars and 200kg/m3 reinforcement rate). To reduce the impact of reinforcement in concrete, there are various alternative reinforcement types that can be used. None of them can be as versatile as the traditional steel reinforcement bars, however in many cases, using one of the following alternative reinforcement types could result in significant embodied carbon savings. The alternative reinforcements can be categorized into organic fibers like hemp fibers, steel fibers which are used widely in various applications like industrial floors, and other mineral fibers or bars made for example from glass and basalt.
The following generic datapoints for alternative reinforcement can be found in the One Click LCA database in addition to the various EPDs developed by manufacturers.
- Bi-component polyester fiber, 100% recycled content
- Hemp fibers, straw, and shives
- Basalt fibers
- Steel fiber for concrete reinforcement, 0% and 100% recycled content
- Glass fiber for concrete reinforcement
- Polypropylene fibre for concrete reinforcement, ranging 0% – 100% recycled content
- Flax fiber
- Jute fiber
- Kenaf fiber
- Basalt rebar for concrete reinforcement
How to find a lower carbon concrete mix in your region
When the time comes to specify the exact concrete manufacturer from where concrete will be procured – usually at detailed design stage or construction stage – how do you find lower impact concrete mixes and manufacturers? One Click LCA’s green material benchmark feature enables you to identify all plant specific mixes that have lower embodied carbon than the one you have already selected. The feature is available either directly from the material query through a material’s data card or via the results page where you can ask One Click LCA to give you a list of more sustainable alternatives to your currently chosen materials.
Find out more about green material benchmarks.
With the Materials Compass you can find and compare asphalt, concrete, and cement materials from around the world.
Who can supply low-carbon concrete solutions?
Many manufacturers are already producing low-carbon ready-mix and precast concrete or cement. All manufacturers that have created EPDs for their concrete mixes or cement products can be found and compared in One Click LCA. Just some of them are listed below for reference.
Europe |
North America |
Middle East and North Africa |
|
|
|
What is the future of circular concrete?
Low or lower carbon concrete is currently made available mostly by replacing cement with alternative binders like GGBS, PFA and silica fume. With the construction industry urgently needing to decarbonize as soon as possible, the demand for such alternative binders is continuously increasing and will increase more in the future. At the same time, the supply of some binders like Fly Ash which is a by-product of coal combustion is set to decline due to the reduced demand of the primary product (e.g. coal based electricity).
Concrete must be made available at even lower embodied carbon than typically achieved now with binders like GGBS and PFA and it must be produced with new innovative manufacturing processes and binders.
In its UK concrete and cement industry roadmap to beyond net zero, the UK Concrete Centre has identified a potential to reduce the embodied carbon of concrete by 39% by 2050 due to the decarbonization of the electricity grid and transportation, lower carbon production of cement and other binders and the switch of the main fuel used in cement production to a renewable fuel. The remaining 61% reduction required for concrete to become a zero carbon material must come via carbon capture technologies which will address mostly the calcination related emissions.
Heidelberg Materials is already building the first Carbon Capture and Storage facility in a cement production plant in Norway and is planning to do the same in another one in Sweden by 2030. Other companies like CarbonCure and Carbonaide as mentioned above reduce the embodied carbon of concrete by using CO2 in the concrete mix itself while companies like Prometheus Materials and Biozeroc are looking into using biotechnology to eliminate the use of cement in concrete to allow reaching a zero or negative carbon building material similar to concrete.
Concrete EPD Generator
Create EPDs for your ready-mix concrete
For concrete manufacturers to create and publish reliable, third-party verified concrete EPDs — fully compliant with global EPD standards.
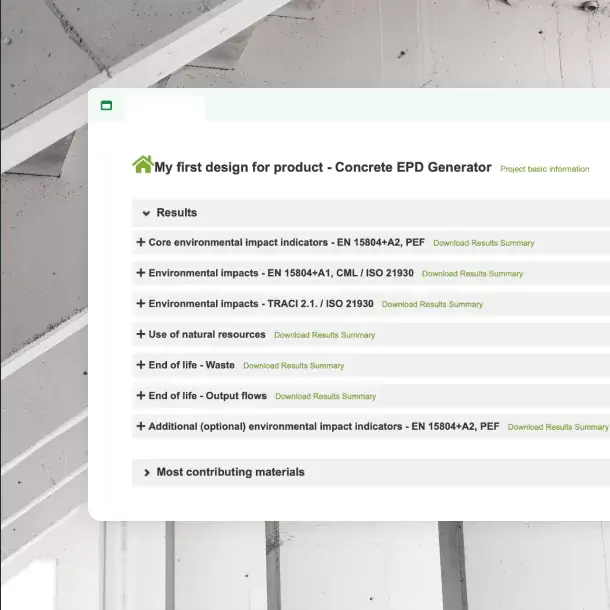
Carbon Experts Newsletter
Industry news & insights — straight to your inbox
Want to learn more?
Marios Tsikos • Feb 08 2024
Melina Zacharia • Apr 16 2024
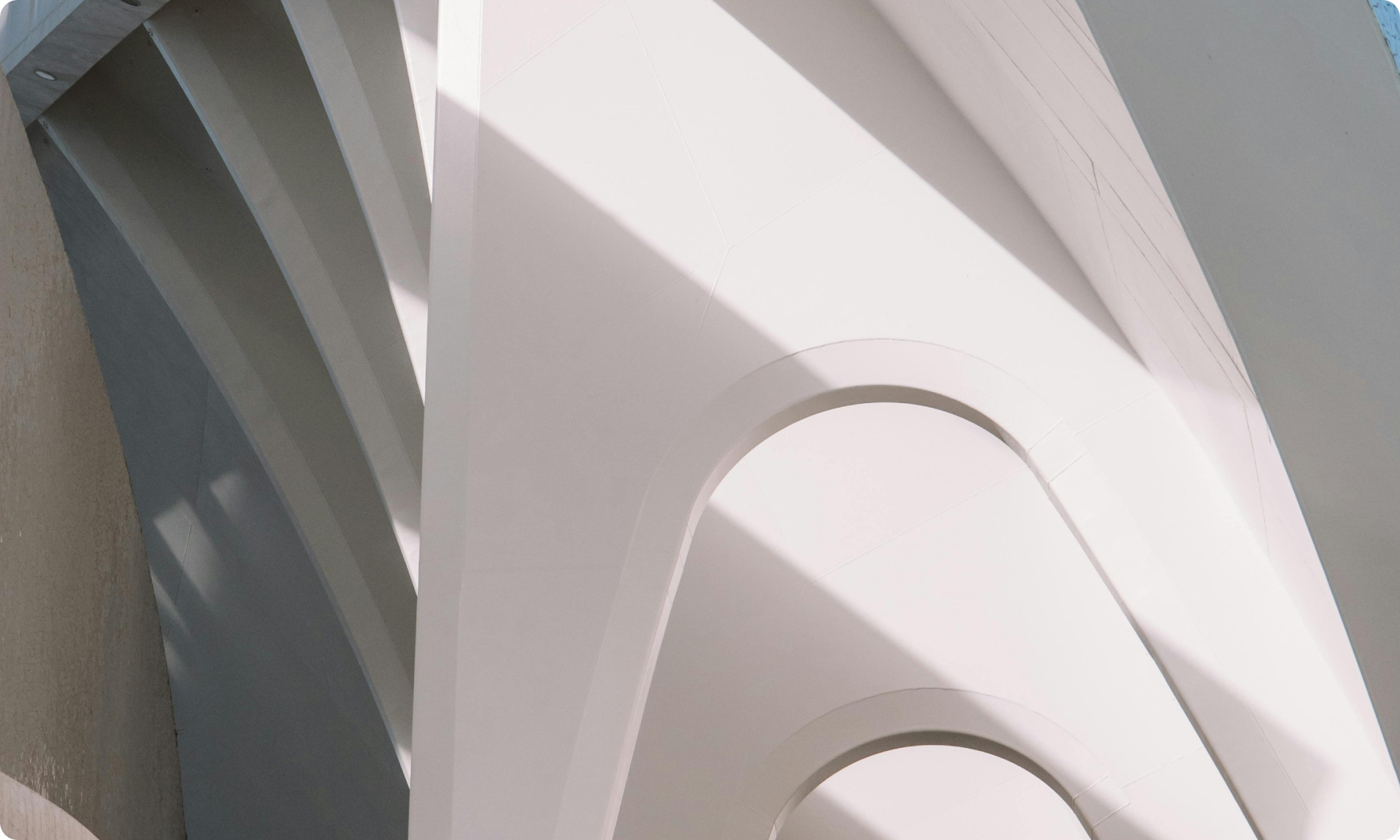
Aileen Carroll • Apr 03 2025
Aileen Carroll • Nov 07 2023