Co-authors: Iñigo Ortiz Diez de Tortosa and Maria Antonia Sabater Terán
The RAMS methodology redefines construction, integrating reliability, safety and efficiency throughout the project life cycle.
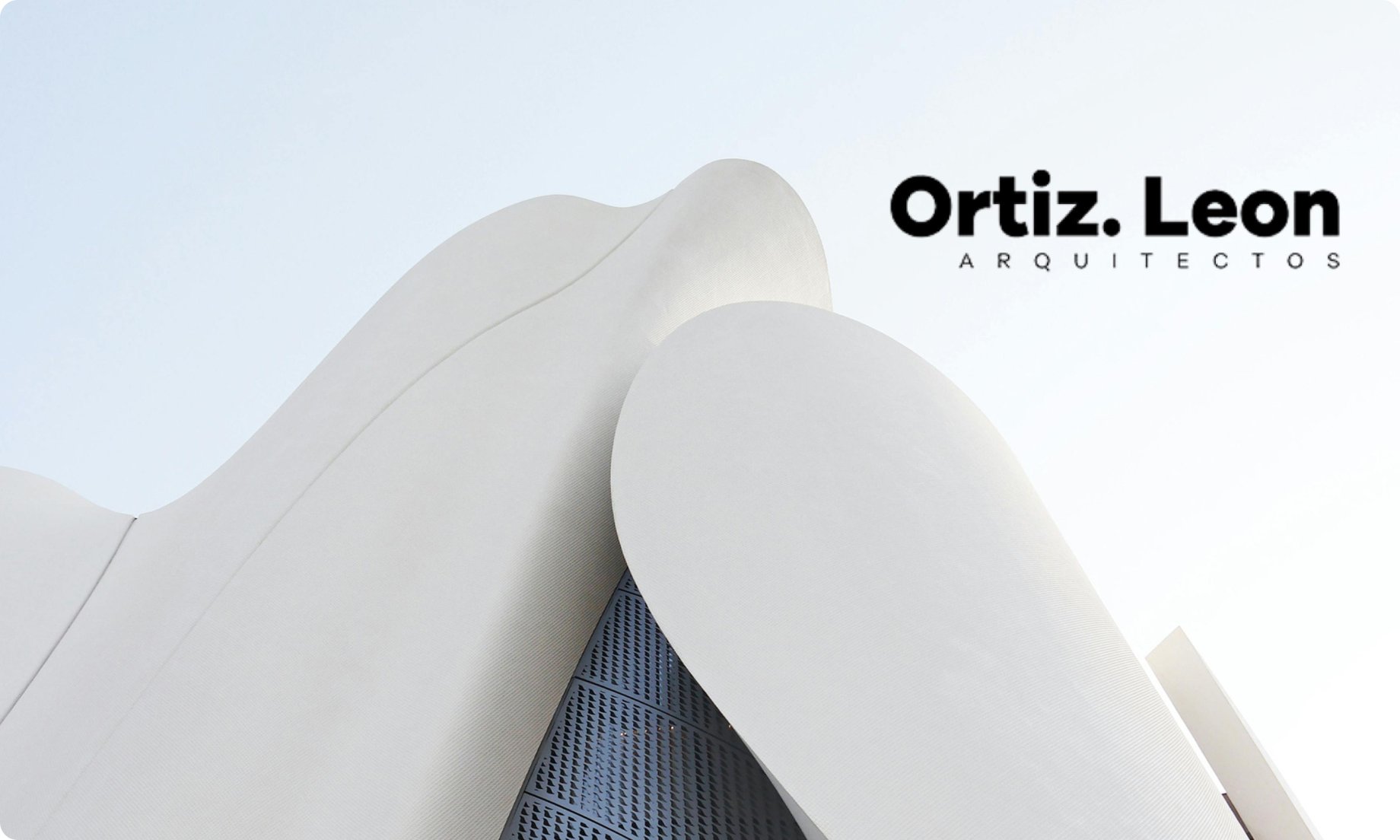
What is RAMS, and why has it not been widely discussed in the building sector until now?
Currently, the future of construction is shifting to prefabrication, where external suppliers manufacture and assemble parts, optimizing resources and minimizing on-site errors. This approach, well-established in the automotive industry, makes it possible to standardize processes, improve efficiency and guarantee greater control over the quality of the final product.
The RAMS (Reliability, Availability, Maintainability, and Safety) methodology provides a comprehensive framework for the design and management of the built environment, ensuring reliability, safety and efficiency throughout the life cycle of a project. Its development dates to the mid-20th century, in sectors such as aerospace and military aviation, where tolerance for error had to be minimized due to the critical risks associated with it. Later, RAMS was adopted in sectors such as rail and energy, where maintenance and system availability are essential for uninterrupted operations. In parallel, the automotive industry began to incorporate RAMS principles into its design and production processes to improve vehicle reliability and optimize vehicle life cycle. These industries showed that proactive management—using failure analysis and asset optimization—can cut costs and improve safety.
Although widely used in technologically advanced sectors, the adoption of RAMS in construction is still in its early stages. Its implementation in construction is gaining relevance due to advancements in digital tools like BIM (Building Information Modelling), the growing demand for sustainability and the need to extend the useful life of buildings under criteria of operational efficiency and climate resilience.
The advancement of digital tools such as BIM has transformed construction project management, enabling more efficient planning and execution. A key part of this transformation is the integration of BOM (Bill of Materials) and the MTO (Material Take-Off) process. A BOM is a detailed document listing all components, materials, and semi-finished products required to assemble a final product, ensuring consistency in production and minimizing errors. Also keeping in mind that the MTO provides a complete list of materials required based on drawings to complete a construction project, including detailed cost estimates for each material. All in all, we realize that together, these concepts allow more accurate management of the resources needed for each project, thus optimizing efficiency and reducing waste.
20+ BIM integrations: One Click LCA’s decarbonization software integrates smoothly into your workflow with advanced data capabilities.
In relation to ensuring operational efficiency and climate resilience, the popularity of integrated contracts, such as DBFM models (Design, Build, Finance and Maintain), has been a key driver in this transformation, extending contractors' responsibilities beyond the construction phase to include maintenance and operation throughout the lifecycle. This approach is aligned with Extended Product Responsibility (EPR), which seeks to ensure that manufacturers and contractors take responsibility for their products and services throughout their entire life cycle.
DBFM contracts: an approach that extends responsibility to maintenance and operation, ensuring long-term sustainability.
The choice to use DBFM contracts depends on factors such as government policies, the availability of financing and the private sector's experience in managing comprehensive projects. In some countries, especially in Europe and North America, DBFM has gained popularity in public infrastructure projects, such as roads and hospitals, due to its ability to transfer risks to the private sector and ensure long-term maintenance. However, there is a growing trend towards the application of this approach in any type of building, extending its scope beyond traditional infrastructure.
In this context, RAMS is set to be a key pillar in the transformation of the sector towards higher standards of quality and sustainability. The combination of its technical approach with tools such as life cycle analysis and digital models allows for more accurate decisions, optimizing resources and ensuring resilient and sustainable buildings over time.
The link between RAMS and LCA: improving efficiency and sustainability
At Ortiz León, advocate the incorporation of the RAMS methodology in the field of building, an approach that, although not yet widely applied in this sector, we believe has great potential. Its integration into construction projects not only improves the reliability and safety of buildings, but also helps to significantly reduce emissions by optimizing the use of resources and ensuring the operational efficiency of systems. This aligns perfectly with tools such as carbon footprint calculation, an analysis that we at Ortiz León Arquitectos perform using One Click LCA.
RAMS, EPDs y LEVEL(s)
The connection of RAMS with life-cycle assessment (LCA) establishes a direct link to Environmental Product Declarations (EPDs). EPDs, as tools derived from LCA, provide accurate and standardized data on the environmental impact of materials, allowing sustainability to be integrated into technical decisions. This integrated approach ensures that buildings not only optimize their technical performance, but also reduce their environmental footprint, promoting solutions that are more durable, efficient and aligned with decarbonization and circular economy objectives.
The linkage of RAMS to the project life cycle makes it a natural complement to LEVEL(s), the European framework for sustainability in buildings. By sharing principles such as operational optimization and resource efficiency, RAMS contributes directly to the six LEVEL(s) macro-objectives. Tools such as life-cycle cost (LCC) analysis and maintainability facilitate decision-making to minimize environmental impact and long-term costs, fostering more sustainable and climate-resilient buildings.
Building LCA made easy: Streamline LCA for construction. Complaint with 80+ global and regional certifications.
RAMS in other industries. Key RAMS tools and lessons learned
RAMS uses key tools such as FMECA, FTA and ETA to analyze risks and optimize designs:
- FMECA (Failure Modes, Effects, and Criticality Analysis): identifies failure modes, evaluates their effects and prioritizes actions. For example, in an HVAC system, it allows to detect critical failures such as loss of compressor operation and prioritize preventive measures. This approach also makes it possible to select components that are more robust and compatible with the project's sustainability objectives.
- FTA (Fault Tree Analysis): Analyzes combinations of failures that can lead to undesirable events. In a skyscraper, it helps, for example, to evaluate the total interruption of elevator service due to motor or backup generator failures, facilitating risk-reducing design decisions. This analysis also helps to optimize energy redundancy systems, improving overall efficiency.
- ETA (Event Tree Analysis): Models the consequences of an initial event. In a curtain wall, for example, it identifies risk scenarios following the breakage of a glass panel, helping to prescribe stronger glass or safer anchorages.
These tools not only improve operational reliability, but also optimize the design from its conception, ensuring decisions aligned with sustainability and long-term performance. Incorporating this type of analysis from the early stages of the project allows anticipating potential failures and mitigating them efficiently, reducing costs and downtime.
RAMS is not just a methodology, it is the pillar for advancing construction towards more demanding standards of quality and sustainability.
Lessons learned: FRACAS and continuous improvement
The implementation of continuous improvement systems such as FRACAS (Failure Reporting, Analysis, and Corrective Action System) reinforce the RAMS methodology by documenting failures, analyzing root causes and providing feedback for future decisions. For example, in the design of a sustainable façade, FRACAS allows problems in sealing joints to be detected during prototyping, thereby adjusting specifications and ensuring that the final solutions are more durable and sustainable. This process is essential for incorporating continuous improvements in projects with high energy efficiency and resilience requirements.
FRACAS ensures that each selected part meets the expected sustainability and quality targets. Furthermore, the detailed documentation obtained through FRACAS allows sharing key learnings with all the actors involved in the construction process, promoting a collaborative and preventive approach.
In addition, data collected through FRACAS is integrated into BIM models, facilitating the creation of historical databases to improve future projects. This continuous improvement cycle ensures that each project represents an advance over the previous one, driving innovation and technical excellence.
FRACAS is aligned with the principles of continuous improvement established in standards such as ISO 56001 or UNE 166002:2021, of R+D+i that we at Ortiz León have implemented in our studio in 2024.
Challenges and strategies for implementing RAMS in buildings
RAMS adoption in construction faces barriers such as:
- Limited knowledge of tools such as FMECA or ETA among designers.
- Resistance to change due to perceived complexity.
- Contracts focused on upfront costs rather than life cycle.
To overcome these, the following strategies should be promoted:
- Training: Equipping designers and operators with RAMS methodologies.
- Digital integration: Using BIM and real-time data for informed decisions. This includes the use of digital twins to monitor system performance in real time and adjust operating strategies as needed.
- Improved contracts: Incorporated RAMS into DBFM models to maximize long-term benefits. Early collaboration with contractors and operators (collaborative projects) is key to ensure that proposed solutions are viable and sustainable throughout the life cycle.
Conclusion and recommendations
RAMS represents a powerful and transformative tool for the building sector, providing a comprehensive approach that optimizes resources, improves safety and enhances sustainability throughout the life cycle of projects. Its adoption requires a paradigm shift that transcends mere technical implementation and focuses on a strategic vision of design, construction and operation.
At Ortiz León, we believe that the future of architecture should be both functional and responsible, integrating methodologies such as RAMS to ensure more reliable and sustainable buildings. The key is to move from design to operation with data-driven decisions, advanced digital tools and a firm commitment to innovation.
This approach is fully in line with the Energy Performance of Buildings Directive (EPBD), which sets increasingly ambitious targets for reducing energy consumption and emissions in the European building stock. Optimizing the life cycle of buildings through RAMS allows not only to improve their reliability and safety, but also to align their performance with regulatory requirements for decarbonization and operational efficiency. In this sense, integrating maintainability, availability and energy optimization criteria in the early stages of design contributes to the creation of more resilient buildings aligned with European climate commitments.
Specific recommendations:
- Implement pilot projects: Focus on buildings with high occupancy or complex technical demands to evaluate the actual performance of RAMS in demanding environments.
- Encourage collaboration: Integrate designers, operators and material suppliers from the earliest design phases to maximize RAMS effectiveness.
- Use actual post-occupancy data: Incorporate information obtained during building operation to refine models and improve reliability and sustainability in future projects.
The challenge lies not only in adopting RAMS, but in making it part of a new way of understanding construction, where each project not only complies with current standards, but also anticipates the future needs of the built environment. On this path, Ortiz León reaffirms its commitment to lead with determination towards an architecture that provides real, lasting and positive value for people and the planet.
Carbon Experts Newsletter
Industry news & insights — straight to your inbox
Want to learn more?
Laura Drury • Mar 24 2025
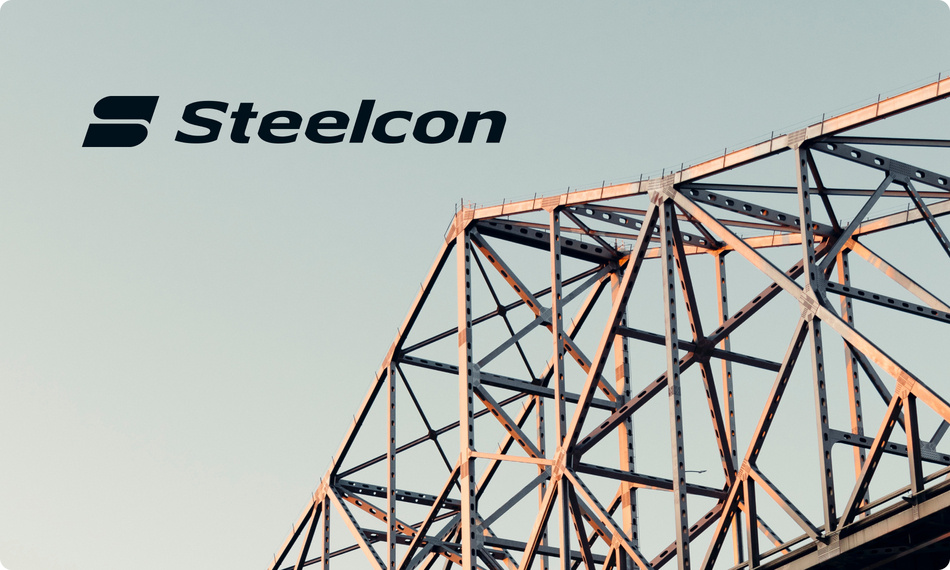
Aileen Carroll • Jan 27 2025
Muhammad Ali Saleem • Jul 23 2024
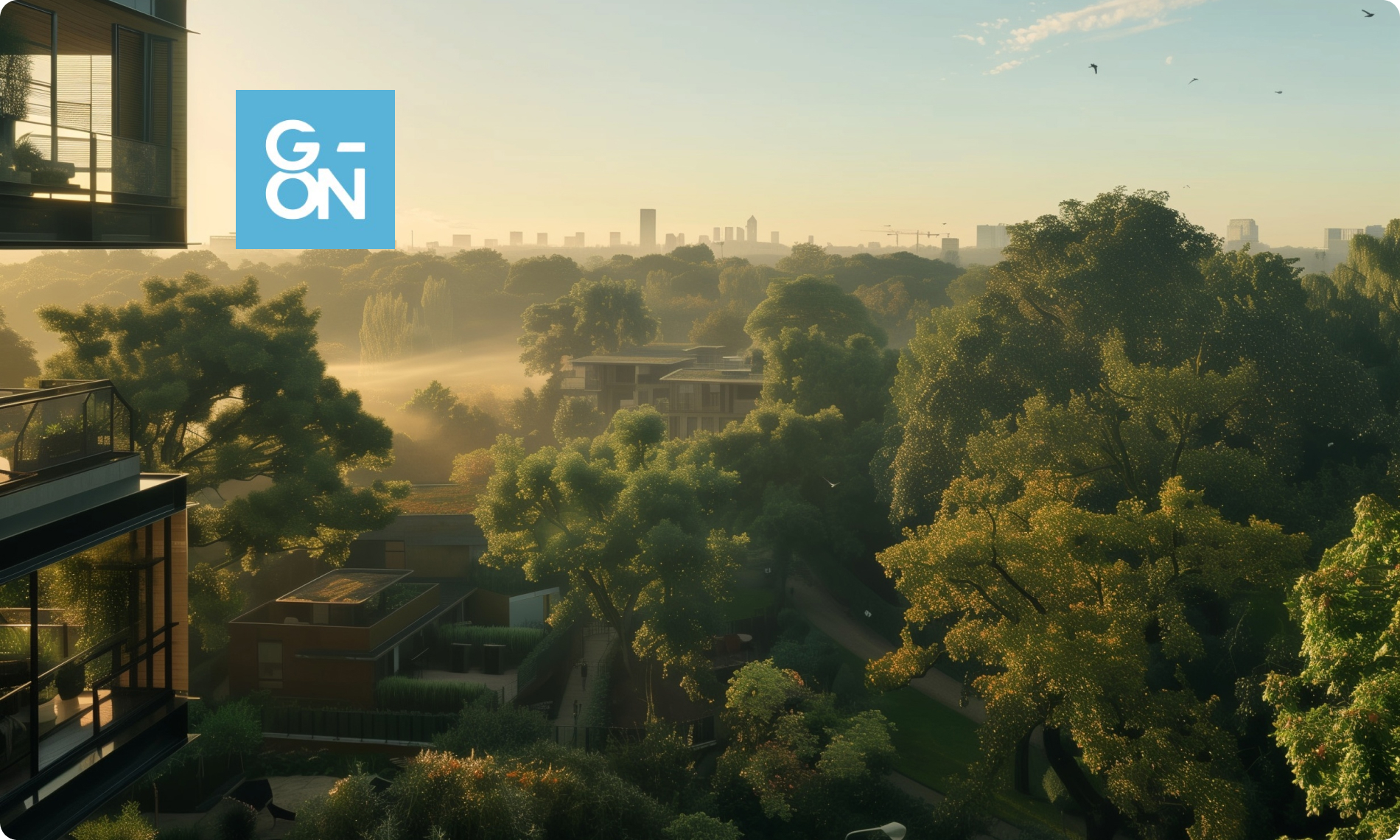
Asha Ramachandran • Jul 03 2025